The real competition in farming is passive: Farmers are at the mercy
of the weather and the markets. Market prices are based on the size
of the harvest and the current availability of corn and beans. If
most producers in the country have a good harvest, the price per
bushel at harvest is low. What a Logan County farmer hopes for is a
high price and a good yield, but that is only accomplished if
farmers in other production areas don't fare as well on yield
because of regional weather conditions. The local farmers aren't
hoping other farmers will fail, but that is the only way to win
passively in the price-per-bushel game. One of the options to
actively hedge is to put a portion of your crop in storage at the
local elevator. The elevator charges a price to dry the grain to
healthy storage levels and a fee per bushel to store the grain, and
the producer gets to choose the time to sell. The downside to
storing at the elevator is that you will sell to that facility, and
there can be a significant difference in bid price between different
co-ops on certain days.
Another active hedge is to store grain on your own farm in your
own storage bins. Exercising this option allows you to capture carry
in the market and expands your marketing opportunities. With your
own storage, you get to choose when to sell and where to sell.
Looking at some of the bins constructed recently, on-farm storage
looks like a costly expenditure, but according to Tyler Haning of
Huffman Farm Supply Inc., most of their customers pay for a bin in
three to five years. In certain years, customers can pay for a bin
in less than one year. Put in those terms, the on-farm storage
option sounds like an affordable way to go.
In addition to being affordable, there are other options on-farm
storage brings a local producer. On-site drying is cheaper than the
elevator charges, and your own grain does not have to be "shrunk" to
14 percent. Drying cost can be only marginally lower, but many think
it is much higher. This is not true; normally individual farmers
will dry for about 60 percent of the elevator charge. This includes
patronage checks or drying cost refunds that some co-ops offer.
Haning says they have definitely seen a change in the drying
trend in last two to three years. Prior to 2009, the trend was
natural-air drying and not being overly concerned about capacity or
expansion.
Recently, continuous-flow dryers have become increasingly
popular. As capacity for on-farm storage rises, farmers are
producing more bushels, harvesting more efficiently and hauling
faster. This has increased the demand for on-farm systems to perform
in more of a "commercial" facility realm. With all these variables
taken into consideration, a continuous-flow dryer is the most
effective and efficient way to dry grain. Farm operations are
growing, and these on-site systems continue to get larger.
Haning said, "This last year we had several customers put up
drying and storage systems, and they had never had either before."
Commercial grain farming has become more of a business instead of
a way of life. Farmers are cutting costs and making money by saving
pennies where they can, while becoming more efficient. Usually, it
doesn't take long to notice the benefits of on-site storage and
drying facilities, especially on the large scale.
[to top of second column] |
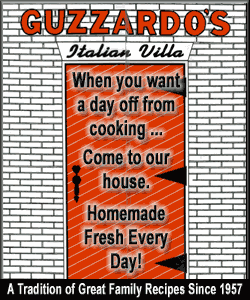
On-farm storage allows farmers to operate longer and farm more
acres because with their own storage, they can run even when the
elevator isn't open. This also cuts down on time and manpower
because your employee isn't waiting in line at the elevator.
You won't find a lot of arguments against the benefits of on-farm
storage. Some producers are shocked at how much more profitable it
can be, and most agree it is more beneficial. It is just a matter of
the extra work and management, and if it suits their operation.
There are a few considerations a producer must make when deciding
about purchasing on-farm storage. The first is that there is more
work involved and more management. Bringing it to the elevator puts
the management of the grain in the hands of the elevator operator,
but on-farm storage means the farmer must maintain what is stored in
his own bins.
This means that the farmer should make a weekly check of the
contents of the bin, and that means climbing to the top to check.
Failure to check the health of the stored crop and the moisture
levels in the bin can cause the whole bin to go sour.
Another downside is that you handle the grain twice (this can
mean extra trucking cost), and many will say that it damages the
grain more. This is marginally true: It is damaged more, but not
significantly, as naysayers believe. And with newer conveying
equipment, the damage is almost completely negated.
Haning says the last advice they always give their customers is
to not just update or right-size for now, but leave room for
expansion in the future. Think several years down the road and give
yourself room to grow.
On-farm storage gives the local producer the ability to shape
their own economic outcome and, in turn, shape the entire industry
by withholding grain from the market when prices are low, thereby
driving prices up. The option to store a portion of your own crop in
your own storage can increase your long-term profitability and puts
you in charge.
[By JIM YOUNGQUIST with information from Tyler
Haning]
|