Yet today, Natuzzi's home base is dragging it down. Best known for
its brand Divani & Divani, the company hasn't made a profit in six
years. In the first nine months of 2013, it lost 38.7 million euros,
deepening year-on-year losses on a slight dip in sales to 328
million euros.
Though it sells in 123 countries, and has factories in China,
Romania and Brazil, Natuzzi says the main reason for his company's
woes is the high cost of making sleek sofas and armchairs at home.
The core of its production and half of its 6,500 worldwide employees
are in Italy where high labor costs and strict employment laws make
it hard for companies to keep up with more nimble competitors
elsewhere.
It costs Natuzzi up to 10 times more to make a product in Italy than
in its factory in China and although it has been proactive opening
factories abroad is under pressure from Italian unions to keep jobs
at home.
The result is that, as the recent economic downturns have hit
Natuzzi's key consumer markets of the U.S. and Europe, the company
hasn't been able to adjust its cost base to compensate for the fall
in consumer spending.
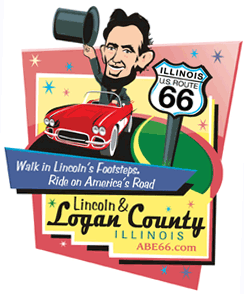
"The orders we have are enough to employ 1,500 people, not our
3,200," the 73-year-old Natuzzi, who is company chairman and chief
executive officer, said in a recent interview in Milan where he was
unveiling the new Revive armchair.
Late last year, Natuzzi agreed to a government-brokered plan that
will allow the company to avoid laying off more than a thousand
workers, while pledging 242 million euros to breathe new life into
the company's Italian operations.
Natuzzi's predicament is just another chapter in Italy's industrial
decline. In the 1980s and 1990s, many Italian companies began
exporting abroad helped by devaluations of the lira that allowed
them to price lower than foreign rivals.
But that advantage was lost when Italy adopted the euro in 1999 — around the same time that European goods faced a flood of
competition from low-cost rivals from China.
Italy's efforts to loosen its labor laws have stumbled, despite
attempts — most recently in 2012 — to make it easier for companies
to adjust their workforce to economic cycles.
Italy's social security and labor taxes are among the highest in
Europe. Despite the 2012 reforms, it is still difficult for
companies to downsize for economic reasons. Usually companies resort
to state-funded furlough schemes in which workers are still employed
by the company and receive a salary, paid largely by the state even
though they don't work.
As a result, many companies, especially in the textile business,
subcontract work to tiny firms to increase flexibility because they
don't fall under the strictest of labor rules or to lower costs
because they hire workers on under-the-table terms in order to evade
taxes.
Until about a decade ago Natuzzi used subcontractors, but — under
pressure from unions — stopped outsourcing its production and now
operates fully-owned plants.
A fire in a factory last month in Prato, near Florence, that killed
seven workers who had been sleeping where they sewed cheap clothes
during the day thrust the spotlight on some 5,000 sweat-shops that
often violate labor and health regulations.
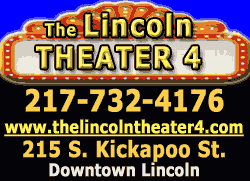
After the fire, Natuzzi wrote a letter to Italy's president,
complaining about "unfair competition" of rivals who use
subcontractors that enjoy little regulatory oversight.
"This is a type of business that seems legal, but that breeds on
illegality. In order to offer products at lower prices, these
subcontractors almost always break the law," Natuzzi wrote in his
letter.
Donato Caldarulo — president of one of southern Italy's upholstery
districts where many of the small subcontractors are based — said in
a statement that while there were some "irregularities" in the
industry, "the respect of legality is something that all the
companies operating in this district hold close to their hearts."
AMERICAN DREAM
Pasquale Natuzzi founded his company in 1959 together with three
friends, but the brand's fortunes didn't really take off until the
entrepreneur began selling in the United States in the early 1980s,
taking advantage of Italy's weak currency to attract buyers in the
world's largest consumer market.
[to top of second column] |

Some 90 percent of the company's production is now exported outside
of Italy, with 45% of its turnover made in the U.S.
In 1993, Natuzzi listed on the New York Stock Exchange, a major coup
that gave its founder — who was dubbed the king of sofa in Italy — added cachet back in his home country.
Paolo Moramarco has been working in Natuzzi's Santeramo maintenance
unit for 22 years. He says the name was enough to get him a mortgage
when he and his wife were buying a house.
"Thankfully, I've finished paying the mortgage because today, if you
show up at the bank with a Natuzzi paycheck, they ask for proof of
another income," he said.
Problems for Natuzzi began in the early 2000s, partly because of the
strengthening euro and because of the global economic downturn that
followed the September 11, 2001 attacks on the World Trade Center in
New York. Between 2007 and 2012, Natuzzi racked up 140 million euros
in losses.
The decline in consumer spending hit much of the furniture industry
of southern Europe. Between 2000 and 2012, the turnover from the
myriad upholstery companies in Puglia and Basilicata regions dropped
to 28.5 billion euros from 42.5 billion euros, according to industry
association Federlegno-Arredo.
Last year, Natuzzi's sales fell to 468.8 million euros from 486.4
million euros the year earlier. In the first nine months of 2013,
sales dropped by 6 percent in Europe, 7% in Italy and 1.5% in the
U.S.
"Our efforts to make our company more competitive at the global
level have been rendered vain," said Natuzzi in emailed answers to
questions.
To balance his high labor costs in Italy, where Natuzzi operates
five of its nine worldwide factories, it has expanded production to
China, Brazil and Romania.
Production costs are 20 eurocents per minute worked in Romania and
10 eurocents in China. But in Italy, where 3,175 employees are
based, the cost has soared to one euro per minute worked — a cost
that is unsustainable, especially compared to rivals in Italy who
use subcontractors that cost a fraction.
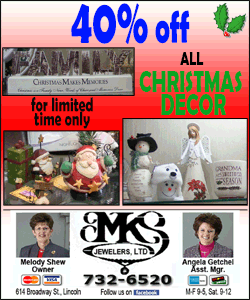
"To be competitive, we would need to get to 50 cents," per minute
worked for our Italian factories, says Natuzzi.
Consofa, a consortium of upholstery makers — was recently fined for
violating labor laws. In a statement, Consofa said that it believed
authorities had "made an erroneous evaluation of its contractual
relationship with subcontractors and suppliers," adding that it was
sure it would "be able to confirm the correctness of our
operations."
Michele Giannelli, who works on the assembly line in Santeramo, says
he can understand fellow workers who accept under-the-table jobs
with subcontractors. "If someone has lost his job, can't rely on
unemployment schemes and faces the bank confiscating his house, then
it's a matter of survival."
Natuzzi's woes in Italy reached fever pitch over the past year. The
company has 1,450 of its workers on Italy's state-run furlough
scheme and last spring warned it would have to begin a collective
lay off scheme because of the worsening economy.
In October of last year, the company reached a deal with unions and
the government in which it will offer buyouts to 600 workers and, in
conjunction, bring part of its Romanian production back to Italy by
creating two new local subsidiaries.
The challenge, Natuzzi says is still to bring down local labor
costs, something the company is looking into.
"We aren't looking for the simplest way out, rather the best and
fairest one," he said.
(Editing by Alessandra Galloni and Anna
Willard)
[© 2014 Thomson Reuters. All rights
reserved.] Copyright 2014 Reuters. All rights reserved. This material may not be published,
broadcast, rewritten or redistributed.
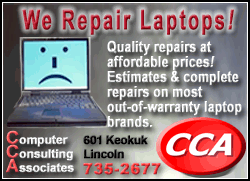 |