As presidential candidates promise to reclaim jobs lost in the
intervening decades, they might want to visit the company now.
Bought by Johnson & Johnson <JNJ.N> in 1981, the fully automated
factory allows four workers to produce in a 12-hour shift what more
labor-intensive methods produced in a year. The Jacksonville plant
and one in Ireland make 4 billion soft contacts a year, and between
the robots and lasers and computer algorithms no worker touches the
product from the start of the process through final packaging.
"I don't think you could even make 4 billion lenses" using the old
method, said David Turner, vice president of research and
development for Johnson & Johnson Vision Care, Inc. "You'd need a
guy with a lathe in every town."
Since peaking at 19.5 million in 1979, the number of U.S.
manufacturing jobs has fallen 37 percent to around 12.2 million as
of March, or just over 10 percent of the private sector workforce.
(Graphic: http://tmsnrt.rs/1WqpioK)
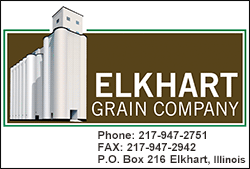
That may be as good as it gets. Despite the promises made on the
campaign trail by Republican frontrunner Donald Trump and other
candidates, the next president will find it hard to raise
manufacturing's share of a U.S. labor force that keeps shifting
toward services.
While much of the jobs debate has centered on trade pacts that
Democrats and Republicans have backed over the last quarter century,
both successful and struggling companies and sectors offer evidence
of long-term trends that neither sharp trade negotiators nor
aggressive political leaders can easily reverse.
Even critics of trade deals acknowledge that labor intensive
industries, such as textiles, which once employed hundreds of
thousands of less-skilled workers, are probably gone for good.
Technology continues to diminish the share of labor in production
and its spread around the world has made other nations - notably
China, but also Korea, Brazil, Mexico and former Soviet bloc
countries - competitive both as exporters and in their own markets.
Investment worldwide is drifting steadily toward services, according
to the United Nations Conference on Trade and Development, and
Americans are spending relatively less of their income on
manufactured goods.
A Reuters analysis of federal data for 1,267 categories of goods
shows that the United States has been running a trade deficit in
more than 500 of them since at least 1992 - before the North
American Free Trade Agreement came into force or China joined the
World Trade Organization, events often cited as turning points for
U.S. manufacturing.
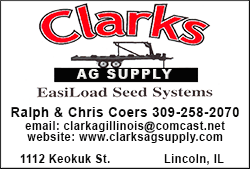
Since the 2007-2009 recession manufacturing has added about 800,000
jobs, but that has lagged overall job growth. As a result
manufacturing's share of private employment has continued to fall,
from about 11 percent since the recession ended.
"The move toward a more global market hurts the marginal,
low-skilled worker, but it was inevitable and you cannot roll it
back," said Brookings Institution senior fellow Barry Bosworth.
At CareerSource Northeast Florida, a job development group,
President Bruce Ferguson, Jr. said by necessity he focused on
finding a "path" for entry level service sector employees to move up
a career ladder, because services are where the growth is.
"The raw (manufacturing) numbers don't look anything like the
service sector and they never will," he said.
VOTER ANGST AND PROMISES
A majority of 6,500 Americans surveyed in March as part of Reuters/Ipsos
2016 campaign polling acknowledged that free trade brings lower
prices, but also saw it as a drag on wages and jobs and an
"important" issue for the next president to confront.
Tapping such concerns, Trump has promised punitive tariffs to "bring
back" jobs for those left behind in the current recovery,
particularly the roughly two thirds of Americans without a college
degree.
[to top of second column] |
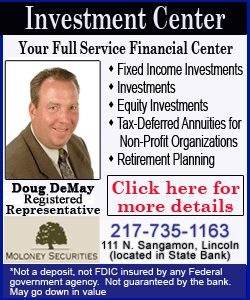
Former Secretary of State Hillary Clinton switched gears as a
candidate to oppose a major Pacific trade deal and promises billions
in public support for manufacturing. Her Democratic rival Bernie
Sanders calls for worker protection against what he considers unfair
trade, while Republican Ted Cruz has focused on trimming government
red tape.
However, playing tough on trade carries some risks and there are
limits to what trade talks and tariffs can accomplish. The U.S.
steel industry is a case in point.
The American Iron and Steel Institute estimates around 12,000 jobs
were lost to a recent jump in imports, mainly from China. It reckons
those jobs could be recovered with steps, such as the anti-dumping
duties imposed by Washington late last year.
That pales, however, in comparison with more than 200,000 jobs that
the sector has lost since the early 1980s, some because of imports,
but some because the amount of labor needed to produce a ton of
steel has fallen from 10 hours to less than two.
"There has been a short term loss that is definitely attributable to
imports, while a longer term trend reflects technological
innovation," said Kevin Dempsey, the institute's senior vice
president.
Such dynamic is not limited to old industries like steel.
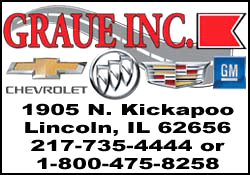
Florida is home to successful manufacturers big and small in a wide
range of sectors, which export nearly half of their output - double
the national average. Yet, as is the case nationally, the share of
jobs available to those with a high school degree has been shrinking
since 2000, according to federal data, and wages have been stagnant.
Johnson & Johnson Vision Care's recent approval of a $300 million
expansion, which added some 100 jobs, cements the company's U.S.
presence, but also shows how technology and innovation reshape the
landscape.
The company's local workforce has risen to around 1,700, but about
60 percent of that are white collar and non-manufacturing jobs -
from research positions for PhD scientists to those in sales and a
highly automated shipping operation.
Florida development officials say the trend is clear: manufacturers
keep cutting the labor content of their products and each round of
investment tends to drive up the skill levels that workers need.
That may benefit the state's economy, but acts as a reality check
for workers who hope that the November 8 presidential vote can
reverse decades-old trends.
"How do you evaluate a company that says we will spend a lot of
money and make the workforce more qualified but not create many
jobs?" said Aaron Bowman, senior vice president for business
development at JAXUSA Partnership, a regional economic development
agency and division of the local chamber of commerce. "Over time you
see more projects that bring in fewer jobs but a bigger bang."
(Reporting by Howard Schneider; Editing by David Chance and Tomasz
Janowski)
[© 2016 Thomson Reuters. All rights
reserved.] Copyright 2016 Reuters. All rights reserved. This material may not be published,
broadcast, rewritten or redistributed.
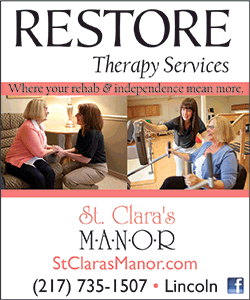 |