Removing excess phosphorus from DDGS before it becomes feedstuff
could alleviate the problem. A new study from University of
Illinois examines the best way to recover phosphorus as a
co-product, which can then potentially be used as fertilizer for
corn and soybean production.
“A lot of phosphorus is in the corn itself. When corn is
processed, you get different products. Some of it is fed in
animal diets, which already contain plenty of phosphorus. So the
additional phosphorus comes out in the manure and leaches into
the groundwater,” says Vijay Singh, the study’s co-author. Singh
is professor of agricultural and biological engineering and
director of the Integrated Bioprocessing Research Laboratory (IBRL)
at U of I.
“We asked, can we do something in the process itself to recover
this phosphorus, and put it back on the land as fertilizer? It’s
like a circular economy,” he adds.
The research is part of a multi-pronged project spanning several
departments in the College of Agricultural, Consumer and
Environmental Sciences at U of I. The project is funded by a
National Science Foundation grant under the Innovations at the
Nexus of Food, Energy and Water Systems (INFEWS) umbrella.
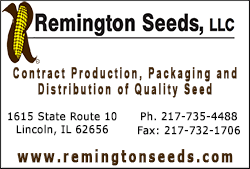
Ankita Juneja, postdoctoral research associate in the Department
of Agricultural and Biological Engineering, is the study’s lead
author. She explains researchers first looked at how phosphorus
flows through the production facility.
“We started with a model and estimated the flow of phosphorous
in the entire diagrammed plant. Then we determined where the
maximum concentration of phosphorus occurs, which will help us
recover it economically,” she says.
The researchers were able to recover 80% to 90% of the
phosphorus through a simple process of increasing the alkalinity
of thin stillage and adding calcium chloride, followed by
stirring the product for five minutes in a continuous stir
reactor.
Juneja explains that the goal was not to remove all phosphorus
because some is needed as nutrients in the feedstuff.
“The animal food requirement of phosphorus in DDGS is 3 to 4
milligrams per gram of DDGS. Previously, the DDGS had about 9 to
10 milligrams per gram. So the rest was all excess, which would
get into the manure. We were able to reduce it down to 3.25
milligrams per gram, which is in the range of what the animals
actually need.”
Removing phosphorus also drains protein from the DDGS, but
Juneja says the study’s recovery process was optimized to ensure
that the amounts of protein and phosphorus left in the DDGS were
calibrated to meet–but not exceed–requirements for animal feed.
The product that is recovered through this procedure is in the
form of a solid precipitate or paste, which contains about 60 to
70% water. It can be dried and eventually used as fertilizer,
though the study does not address that process. Singh says that
is currently being tested by scientists in the U of I Department
of Crop Sciences.
“We have clearly shown that you can recover this phosphorus from
a processing plant so that it doesn't go in different
co-products such as animal feed,” he notes.
[to top of second column] |
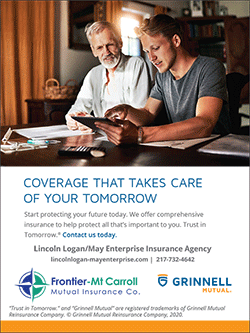
The researchers evaluated both the technical and
economic aspects of the recovery process. While processors do have
to invest in new equipment to perform the separation, there is the
potential for selling the recovered co-product as P fertilizer for
corn and soybeans.
“We did the economic analysis of how much it would
cost to add the recovery section in an existing dry grind plant: how
much it would cost in terms of fixed cost; how much it would cost in
terms of operating costs every year; and how much extra revenue
could be generated by producing this extra co-product, which can be
used as fertilizer or other applications,” Juneja explains.
“We found that the additional investment was $5.7 million in an
existing dry grind plant that produces 40 million gallons of ethanol
a year. The amount of added revenue is a little less than a million
dollars each year,” she adds.
Plants are not currently implementing these practices, but
processors are very interested in learning about the study’s
findings, Singh notes.
“They want to know how to do it. Even just providing them with
information on how phosphorus flows in their plant is a lot of
value. And then giving them strategies to recover it; that is also
of value to them,” he adds.
Singh says this is the second of three studies he and Juneja are
conducting on phosphorus recovery as part of the INFEWS project.
“We are looking at three different refineries within the Upper
Sangamon Watershed,” he says. “In this watershed, there are many
different processing plants because Illinois has lot of bean and
corn processing.”
The first study looked at corn wet milling plants, where corn is
converted to starch for making high fructose corn syrup, and the
third study will focus on soybean processing plants.
The article, “Recovering the phosphorus as a coproduct from corn dry
grind plants: A techno-economic evaluation” is published in Cereal
Chemistry. [doi.org/10.1002/cche.10260]
Authors include Ankita Juneja and Vijay Singh, Department of
Agricultural and Biological Sciences, and Roland Cusick, Department
of Civil and Environmental Engineering, University of Illinois.
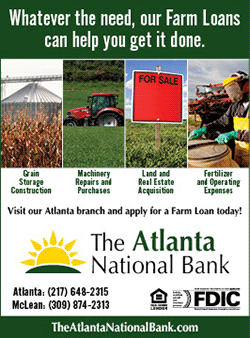
The first study, “Techno‐economic feasibility of phosphorus recovery
as a coproduct from corn wet milling plants,” was also published in
Cereal Chemistry. [doi.org/10.1002/cche.10139]
Authors include Ankita Juneja, Navneet Sharma, Roland Cusick, and
Vijay Singh.
Funding for both studies was provided by the National Science
Foundation, Division of Earth Sciences.
[Sources: Ankita Juneja, Vijay Singh
Writer: Marianne Stein] |