U.S. producers undo years of efficiency gains in fight for supplies
Send a link to a friend
[May 10, 2022] By
Timothy Aeppel
(Reuters) - U.S. manufacturers are finding
that their main weapon to fight supply chain snarls is greater
inefficiency.
Industrial companies reporting earnings over the past few weeks have
described steps they've taken - from acquiring trucks to move their own
goods to building products that sit around on factory floors waiting for
missing semiconductors - to deal with delays and shortages that have
dogged them over the past year.
"We want to optimize our supply chain to its fullest," said John
Morikis, chief executive of Sherwin Williams Co, describing to analysts
last month how the Cleveland-based paint maker has started using its own
trucks - a much costlier route than using third-party services - to get
around bottlenecks in transport systems.
Morikis admitted this is "less efficient," but necessary to meet surging
demand. Over time, he said, he hopes "the efficiency will work its way
back."
There are few signs that will happen any time soon. A recent study by
Royal Bank of Canada concluded that one-fifth of the global container
fleet is stuck in congestion at ports around the world. The report said
supply chain problems seem likely to worsen as China's COVID-19
lockdowns spread and Russia's invasion of Ukraine disrupts trade flows.
Shipping products from a warehouse in China to a facility in the United
States currently takes 74 days longer than what was usual pre-pandemic,
according to the report.
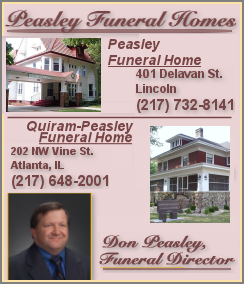
FAR-FLUNG AND FRAGILE
Supply problems have helped drive up inflation - making it a focal point
for the Federal Reserve’s efforts to cool the economy. The Fed last week
raised its benchmark overnight interest rate by a half percentage point,
the biggest jump in 22 years, and said it would start cutting back on
its bond holdings next month as a further step in the battle to lower
inflation.
In recent months, Fed officials have described pandemic-related supply
chain problems, compounded by a restructuring of global energy flows in
the wake of Russia's invasion of Ukraine, as a force that could lead to
persistent inflation. Patrick Harker, president of the Philadelphia Fed,
in March described the growing realization among policymakers that
global supply chains have grown too far-flung and fragile, posing risks
to economies.
"We thought this would go away," said Harker, as the impact of the
pandemic fades. But "these waves keep hitting us and keep damaging
supply chains."
For decades, manufacturers pushed to develop lengthy supply lines that
spanned the globe, usually targeting the least expensive sources of
goods, particularly in China and elsewhere in Asia. The search for
low-cost sources became a key part of "just-in-time" systems, in which
companies kept only the minimum stock on hand to feed current production
and emphasized flexible supply contracts and economies of scale.
"I do not think we're going to pull back supply chains completely," said
Cliff Waldman, the chief executive of New World Economics, an economic
analysis firm that studies manufacturing trends. There are too many
benefits to those global networks, he said.
[to top of second column] |
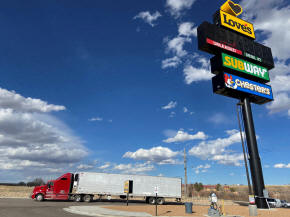
A truck pulls into a truck stop in Las Vegas, New Mexico, U.S.
March 23, 2020. REUTERS/Andrew Hay
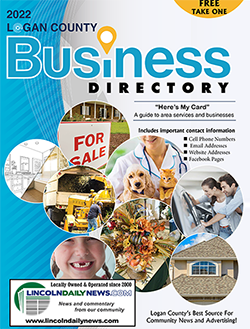
"We want efficiency, because higher efficiency means lower cost," he said. "But
companies don't want efficiency at the expense of excessive risk."
'WE NEED A BUFFER'
Many companies focused on how they were responding to these problems in their
earnings calls. In many cases, the moves add to costs and complexity in their
systems.
Rockwell Automation Inc, the Milwaukee-based maker of factory software and
automation equipment, said one response to shortages has been to build more
products that had to wait for scarce semiconductors to be finished.
"That's one reason we saw our working capital increase in the (latest) quarter -
as we had a higher amount of product being built in anticipation of getting
chips," Blake Moret, Rockwell’s chief executive told Reuters. Moret said he
considers many of the efficiencies created by shortages to be part of a new
normal.
The good news for Rockwell, he said, is that recent disruptions are pushing more
companies to move production to new locations, to help insulate themselves from
future shocks. Rockwell expects to gain more business as it supplies those new
operations with automation equipment, said Moret.
Aaron Jagdfeld, chief executive of Generac Holdings Inc, said supply chain
disruptions have meant having to "pay through the nose to expedite things - a
lot of air freight."
To speed up truck deliveries, meanwhile, the Wisconsin maker of backup
generators has employed "team driving" to get badly needed parts quickly across
the country from West Coast ports. Those trucks employ two drivers - allowing
them to take turns sleeping to avoid mandated stops.
"You're paying for two drivers for one load," said Jagdfeld.
He thinks these types of logistics costs will eventually ease as transport
systems return to normal and prices come down, but many of the other changes
made to Generac's production systems are here to stay, he said. For instance,
Generac has worked on finding second and third suppliers for more of its parts -
seeking them in multiple regions of the world - more costly than relying on one
source but, he said, more secure.
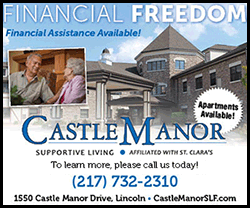
"What we've learned is that we need a buffer," said Jagdfeld. "The way we'll
create that is by carrying more inventories of the component supplies we
consume."
(Reporting by Tim Aeppel; Additional reporting by Howard Schneider; Editing by
Dan Burns and Andrea Ricci)
[© 2022 Thomson Reuters. All rights
reserved.]This material may not be published,
broadcast, rewritten or redistributed.
Thompson Reuters is solely responsible for this content. |