Some of the plates, or gussets, also may have been weakened by welding work over the years, and some may have been too thin or too small, engineering experts said Thursday.
The National Transportation Safety Board, in a brief Wednesday advisory to states to check such plates in bridges nationwide, cited a "design issue" with the bridge's gussets. Engineers say that the plates are an obvious place to start looking, but that a number of other factors might have contributed to the Aug. 1 collapse that killed at least seven people and left at least six still missing.
On Thursday, NTSB officials said "people have run maybe a little bit too far" with the statement on the gussets.
"Simply by finding a piece of metal that's been sheared or twisted doesn't necessarily mean it's a critical piece of the puzzle," said Bruce Magladry, director of the NTSB's Office of Highway Safety. "We see a lot of steel that's damaged because of the bridge collapse. What we need to ferret out is what's an initial cause of damage vs. what's a secondary cause."
Engineering experts said failure of the plates, which usually sandwich the bridge's steel beams where they intersect, in a critical spot could have brought down the whole bridge, although no one has pinpointed a gusset as the cause of the failure.
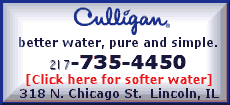
"What they'll be looking for is to see whether one of the gusset plates may have fractured," said W. Gene Corley, a forensic engineer with the Skokie, Ill.-based engineering firm CTL Group. "If one of those gusset plates breaks, then you have lost half the strength at that location, and most likely the other one can't carry the load then."
The bridge's builders in the mid-1960s riveted the plates together, which required many more holes than bolts would have. More holes weaken steel, said Abolhassan Astaneh-Asl, a professor of structural engineering at the University of California-Berkeley, who compared them to Swiss cheese.
The rivets also tend to slip more than bolts and can lead to more cracking, Corley said. Bolts are preferred in modern bridge construction, and were used in more recent repairs.
Welding work on some gussets -- at temperatures of 2,600 degrees or more
-- could also have caused tiny cracks to form as superheated steel cooled, which may have developed fatigue cracks.
Astaneh-Asl reviewed 1965 construction drawings of the bridge that showed varying thicknesses of the gussets. Some in key spots over the Mississippi River were only a half-inch thick, he said, and his rough calculation of the pressure they could withstand suggested they were weaker than the beams they connected. A cracked gusset is visible in photographs taken after the collapse, he said, but it's unclear what role that might have played in the bridge's failure.
[to top of second column]
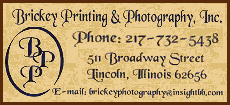
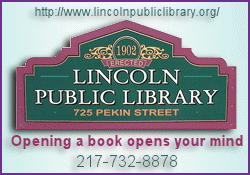 |
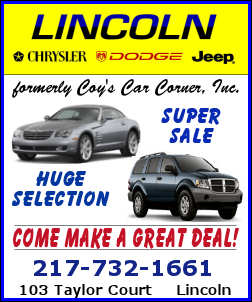 State transportation officials say damage seen on the bridge's gussets might have been caused by the collapse.
Various problems in the bridge may simply have added up over the years and created stresses that the designers never contemplated, Astaneh-Asl said. For instance, at least one expansion joint locked up, possibly pulling one of the bridge's piers out of alignment and leading to undetermined pressures on other parts of the bridge. Such things could have made fatigue cracks worse, he said.
Inspectors who completed the bridge's last full inspection in June 2006 noted problems
-- "section loss, pitting, heavy flaking rust" -- on several of the plates. They also reported loose bolts on another gusset.
Corley, who has been invited to be part of a private investigation into the collapse, said he saw "lots of rust" on the gussets.
"It brings the issue of load and brings the issue of fatigue there as well as corrosion," he said.
But something could have gone wrong in design, too, Corley said. Each plate is individually designed, and someone could have miscalculated the load or weight-bearing capacity of an individual gusset plate, he said.
"In design there's always the chance for a blunder," Corley said. "One of the most common causes of collapse of any type of structure is the blunder."
Investigators are looking closely at the weight that was on the bridge when it fell.
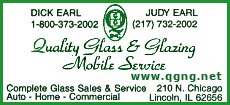
Construction crews had piled up sand and gravel on the bridge as they prepared to pave a 520-foot stretch of two southbound lanes of the freeway, said Liz Benjamin, a construction engineer with MnDOT. Equipment on the bridge included a cement truck, a concrete mobile mixer, buggies to haul the concrete and personal vehicles of the workers. Workers also were using 45-pound jackhammers to remove the top layer of pavement.
The bridge was one of Minnesota's busiest, carrying 140,000 vehicles a day. Mark Hallenbeck, director of the Washington State Transportation Center at the University of Washington, said that's dramatically higher than designers would have considered in 1965.
The traffic would have contributed to fatigue over the years, Corley said. But the weight of truck and vehicle traffic is "pretty insignificant" next to the weight of the bridge itself, he said.
[Associated Press; by Martiga Lohn]
Associated Press writers Patrick Condon in Minneapolis and Seth Borenstein in Washington contributed to this report.
Copyright 2007 The Associated Press. All rights reserved. This
material may not be published, broadcast, rewritten or
redistributed. |