More at home on a pizza, mushrooms certainly aren't a typical building material, but Bayer thought they just might work when given the assignment two years to create a sustainable insulation.
Combining his agricultural knowledge with colleague Gavin McIntyre's interest in sustainable technology, the two created their patented "Greensulate" formula, an organic, fire-retardant board made of water, flour, oyster mushroom spores and perlite, a mineral blend found in potting soil. They're hoping the invention will soon be part of the growing market for eco-friendly products.
Bringing the insulation to market is still at least a year away though, said McIntyre, and will require much more research and work, not to mention more sophisticated equipment and a better work space.
"We've been growing the material under our beds," said McIntyre, adding that they've applied for a grant from the National Collegiate Inventors and Innovators Alliance.
The two young developers -- Bayer is 21, McIntyre 22 -- graduated in May from RPI with dual majors in mechanical engineering and product design and innovation.
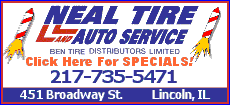
"I think it has a lot of potential, and it could make a big difference in people's lives," said RPI Professor Burt Swersy, whose Inventor's Studio course inspired the product's creation. "It's sustainable and enviro-friendly, it's not based on petrochemicals, and doesn't require much energy or cost to make it."
The two say recent tests at the National Institute of Standards and Technology have shown it to be competitive with most insulation brands on the market. A 1-inch-thick sample of the perlite-mushroom composite had a 2.9 R-value, the measure of a substance's ability to resist heat flow. Commercially produced fiberglass insulation typically has an R-value between 2.7 and 3.7 per inch of thickness, according to the Oak Ridge National Laboratory in Tennessee.
With a rapidly increasing global population, a limited supply of natural resources and rising energy prices, eco-friendly housing products are selling fast. Numerous companies have carved out their niche selling "green" building supplies such as recycled fiber board and plant-based paints. The Environmental Home Center in Seattle sells an insulation made from denim scraps and another made from 100 percent recycled paper among their many green building products.
After looking through about 800 patents, though, Bayer and McIntyre realized they'd hit upon a relatively original idea. Unlike many green building products, Greensulate isn't made from pre-existing materials. It requires little energy or expense to produce because it's grown from organic material.
[to top of second column]
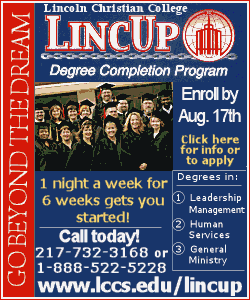 |
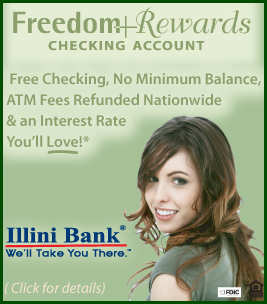 Here's how it works: A mixture of water, mineral particles, starch and hydrogen peroxide
is poured into 7-by-7-inch molds and then injected with living mushroom cells. The hydrogen peroxide is used to prevent the growth of other specimens within the material.
Placed in a dark environment, the cells start to grow, digesting the starch as food and sprouting thousands of rootlike cellular strands. A week to two weeks later, a 1-inch-thick panel of insulation is fully grown. It's then dried to prevent fungal growth, making it unlikely to trigger mold and fungus allergies, according to Bayer. The finished product resembles a giant cracker in texture.
"It really allows for a myriad of uses," said McIntyre. He said they've envisioned modifying the product to make structural panels that could be grown and assembled onsite to produce sustainable homes.
"Green building materials should be evaluated on the idea of cradle to cradle," said Evelyne Michaut of the Natural Resources Defense Council.
In the cradle-to-cradle industrial model, goods should either be fully biodegradable or reusable, limiting waste and pollution, according to Michaut, a sustainable city advocate from Santa Monica, Calif.
"That's the ultimate environmental reference," she said, adding that it seems like Greensulate is on its way to fulfilling that criteria.
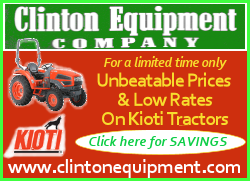
For Bayer and McIntyre, their next step will be creating larger pieces of Greensulate to use in building a wall. From there, they'll perform further testing to see how the product stands up to various elements, including saturation and humidity. McIntyre said they have one two-year-old sample that's been exposed to the elements and shown no sign of degradation.
As part of their development plan, they're entering a new business incubation program at RPI to get their company, Ecovative Design, off the ground. Eventually, they hope to land a partnership with another company.
"Our biggest challenge is that while we have this technology, we still have a lot of research to do," said Bayer. "The key is to really make sure we have a product that is mature and robust before we bring it to the market."
___
On the Net:
[Associated Press] |