Then they have to scout out breeding stock. Then they have to plan the spring hatch. Then they have to manage growth through the summer heat. And by late fall, it's time for another holiday harvest, when they sell more than half of the 20,000 turkeys they raise each year.
The same cycle plays out annually across New England at the dozens of family-owned turkey farms offering an alternative to commercial processors.
"People just see how busy this is this week," Rischer's wife, Patt, said as the first customer arrived at 6:20 a.m. "It's busy all year."
There were no complaints from her son, Jamie, sporting a pair of work gloves and bundled against the outdoor cold.
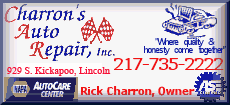
"I love the excitement," he said. "It's a rush for me."
Associate Agriculture Commissioner Scott Soares said Massachusetts also gets a jolt from the activity.
"With that surge comes the additional employment opportunities," he said. "They bring in part-time help to get them through this holiday rush."
Recent video of Alaska Gov. Sarah Palin holding a news conference while a turkey grower slaughtered his birds in the background created an Internet sensation. Here, birds roam in covered pens, their concrete floors buried beneath wood shavings, food and water available in automated bins.
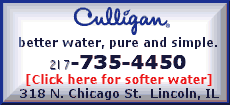
When it's time for slaughter, the turkeys are knocked out with an electrical charge before being processed by both hand and machine.
Raymond's started in 1950, when Raymond and Claire Rischer, a plumber and nurse, were given two dozen birds by one of her grateful patients. The couple were interested in working for themselves, so they decided to raise the turkeys.
They expanded their flock as they moved from the family's garage to a 100-acre former dairy farm near the New Hampshire state line. Raymond has since died, but Claire lives in the farmhouse attached to the red barns and concrete silo that make the farm a local landmark.
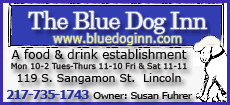
It is now run by their son and his wife, Jim and Patt, and their three children, Jamie and sisters Vickie and Kim. And Vickie's 17-year-old son, Chris, is part of the fourth generation. The high school senior skipped classes the early part of Thanksgiving week to help at the sales counter.
"I've been working around here since the third grade," he said. "Whenever there wasn't a baby sitter around, they'd say, `Go down to the farm.' There was always something to do here."
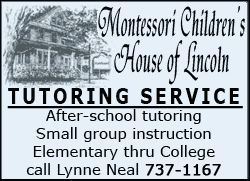
Jim and Jamie are in charge of the birds, and they have to carefully calculate the egg-laying and egg-hatching to ensure a steady supply of birds and to meet the peak demands at Thanksgiving, Christmas and Easter.
Eggs are incubated in a room with precisely controlled temperature and humidity, the latter important so chicks can poke through a tender shell. Chicks then move to a room with a floor whose temperature is lowered weekly in 5-degree increments to ensure the birds transition properly to the outdoors. Then they're moved to the pens, where they are separated by age and sex and fed a diet that changes every four weeks.