Now, the married, minivan-driving father of a small child is a weed guy -- one of the dozens of Washington state workers involved in the creation and regulation of the nation's first legal marijuana industry.
So he spends his days studying a substance that until recently he knew almost nothing about, beyond the few joints he smoked in college. It feels like cramming for a final exam, he says.
"It's very surreal," Steenhout said recently as he stood in a darkened room full of blossoming pot plants. "I generally go to work fairly early, around 6:30 or 7, and leave about 5 or 6, and I'm pretty much talking about marijuana in one way or another every single hour."
Steenhout's cannabis crash course could be for naught if the U.S. Justice Department sues to keep legal pot sales that Washington and Colorado voters approved last fall from taking effect. Marijuana remains illegal under federal law.
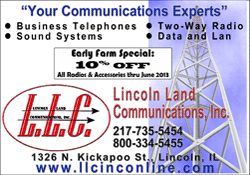
In Washington, voters legalized pot for adults over 21 and set up a system of state-licensed pot growers, processors and stores.
The state has hired a Massachusetts firm to serve as its official marijuana consultant, but the Liquor Control Board, which collects taxes and fees from booze sales and licensing, is also doing its own research into how to best regulate pot.
Steenhout, the agency's comptroller, has new duties that include researching quality assurance: how the pot can be produced, processed and tested to ensure the final product doesn't have contaminants such as mold and that there is a consistent potency when it reaches store shelves.
His research will help inform the board's three voting members as they decide what to require of the industry. All rules need to be finalized before the agency begins issuing licenses to retail stores in December.
Steenhout is traveling to marijuana grow operations, processors and testing labs in California, Colorado and Washington.
On his cellphone, he keeps video of a massive, 75,000-square-foot marijuana grow he visited in Colorado that he uses to impress the folks at the smaller Washington operations.
One morning recently, dressed in a green sweater, jeans and sneakers, Steenhout walked into a first-floor office in Seattle's University District
-- the Care Wellness Center, a clinic that writes authorizations for medical marijuana patients.
Steenhout was there for presentations from Cale Burkhart, who makes marijuana-infused lotions, creams and tinctures, and from the proprietors of Analytical 360, a Seattle lab that tests marijuana and marijuana products for strength and impurities.
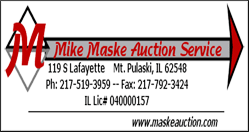
Clear glass mason jars filled with dried marijuana flowers, leaves and a viscous brown liquid
-- pot-infused, vegetable-based glycerine, a potent tincture that can be taken under the tongue with a medicine dropper
-- were lined up on a table as Burkhart spoke.
He described how the lab tests the strength of his infusions, and then gives him a formula to determine how much more glycerine he needs to add to dilute the tincture to its desired potency, 75 milligrams per fluid ounce.
Burkhart keeps records for every batch noting how it was made, at what temperature the glycerine was infused, how strong it was before dilution and other details.
Steenhout took notes on a white legal pad in a folder on his lap, examined small jars containing Burkhart's products, such as a muscle-and-joint rub made with pot, mint oil and cayenne pepper, and asked questions that betrayed how far his education has come.
[to top of second column] |
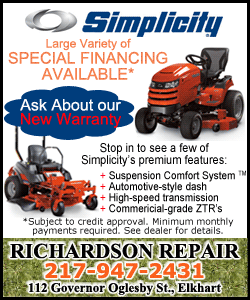 Should the recommended serving size vary among tinctures and other types of edibles, such as brownies or drinks?
What should the minimum qualifications be for lab workers who sign off on marijuana quality-assurance tests?
Does Analytical 360 just use standard lab procedures from the United States Pharmacopeia, or from overseas compendia as well?
"Oh my Gosh, he's grown so much," noted Greta Carter, the clinic's owner.
About an hour later, Steenhout was inside a red, two-story building fenced with barbed wire in industrial South Seattle
-- a marijuana grow operation that helps supply the Conscious Care Cooperative, a medical marijuana collective with 8,000 patients.
He was surrounded by hundreds of pot plants of various sizes, but seemed most impressed with the few pages of a document describing the grow-op's standard procedures
-- what nutrients the plants are given and when, when foliage sprays are applied.
"See, this is useful," Steenhout said. "I've been thinking a lot about GMPs, you know"
-- good manufacturing practices.
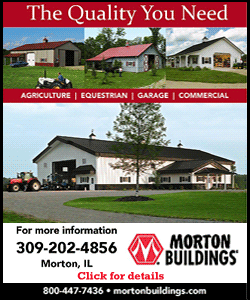
In another room, Jim Andersen, with a company called XTracted, showed Steenhout how he uses a closed-system extraction device
-- a contraption of metal cylinders and tubes -- to make hash oil from marijuana buds or leaves.
The system uses a vacuum to inject and then completely remove the butane solvent from the product, and virtually eliminates the risk of explosion because no oxygen is introduced, he said.
Andersen pulled several types of hash oil out of a black plastic tub to show Steenhout, and offered to send him home with some samples. Steenhout politely declined.
"I get that all the time," he said later. "These people are proud of what they do."
After one final stop at a Seattle business park, to visit a company that makes extraction systems, Steenhout was ready to drive back to Olympia. He was asked whether, after his months of work, he planned to buy marijuana from a state-licensed store once it's available.
"I have no idea," he said. "I haven't really thought about it."
[Associated
Press; By GENE JOHNSON]
Johnson can be reached
at
https://twitter.com/GeneAPseattle.
Copyright 2013 The Associated
Press. All rights reserved. This material may not be published,
broadcast, rewritten or redistributed.
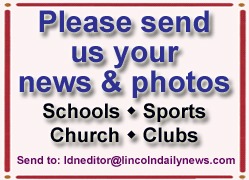 |