Earlier this year, Central Illinois Ag of Atlanta hosted a
combine clinic to show off some of the newest gadgetry and drive
home a big lesson to local farmers. Today farming is about
knowledge, and technology is putting knowledge at the fingertips of
the producer, literally.
Throughout the morning, various Case-IH experts talked about new
combines coming out, new monitoring systems and the duties that can
be performed from the cab; among those was the evolution of the
Yield-sense technology.
From the cab of the combine, the producer can monitor yields on an
acre-to-acre basis or even hopper-to-hopper, can measure the
moisture of the corn going into the hopper, can map the fields by
zones, and can track the harvest by hybrid, all with a few pokes of
buttons. And it all occurs in real-time as it is computed through
the Cloud.
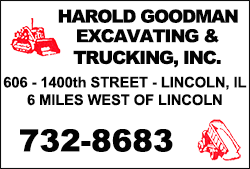
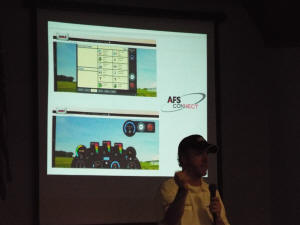 But it isn’t a matter of push a button and everything is all set.
There are steps involved in the set up that have to be followed
precisely and in a particular order.
In the new generation of combines and technology, one new
development is an automatic set on the header height. The height is
set through a calibration process in the field. The header height is
important in the monitoring of yields. During the CIA presentation,
the discussion included how to do this calibration properly.
In order for the new generation of monitors to do their job, the
equipment has to be calibrated starting with the header. Today’s
headers have sensors built in that will tell the monitor in the cab
what head is on the combine.
Once the head is mounted, the hydraulics and electrical hooked up,
the operator needs to calibrate the header height for two positions,
cutting, and not cutting. When the combine is moving down the field
with the head at the cutting height, the sensors and monitor are
working to measure distance traveled and product going into the
hopper. Using these two measurements the monitor can then calculate
the yield in real time in the field.
When the corn head raises at the end of the row, the sensors in the
head communicate to the monitor that it is time to stop measuring
distance traveled. This is a key component of measuring the yield,
and it is important that the header be raised to the proper height
at the end of a pass.
Another important calibration is the sieve calibration. Again this
is done once. First set the sieve, for example, to a quarter of an
inch top and bottom. Then in the cab follow the step-by-step on
screen instructions to set the monitor to show that accurate sieve
setting. A similar calibration is also done for the concaves.
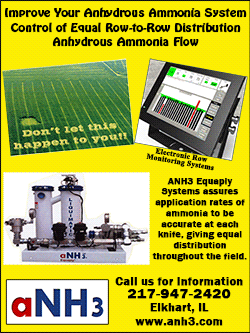 With today’s technology, the farmer can also analyze his crop on the
move. The newest systems are now capable of monitoring grain
moisture in the field as the corn is being shelled. The first step
to achieving this is to collect a physical sample of the corn going
into the hopper, and run it to the local elevator for a soil
moisture test. There is no need to stop and wait for the results to come back. The
test can be done at the elevator; the results brought back to the
combine and put into the onboard computer system. The system will
then take that moisture test and apply it to the sample load. In
essence, that load then becomes the control. The computer will then
compare the control to loads shelled later, and calculate a moisture
content on everything that has been harvested thus far. The computer
will continue to use that original sample as the control until it is
given a new sample results to work with, and it will all be done in
real time.
With this year being a late wet harvest, this is a valuable tool to
the producer. Moisture testing in real time can help the producer
make the decision to go on or go home. As we enter November with
harvest still ongoing the option to go home is going away, but the
tool can help in other areas as well.
Grain producers will probably do more storage this year due to the
low price per bushel on the cash market right now. Corn can be
directed to drying bins and holding bins according to moisture.
Coupling all wet corn together in one place, and all the dryer corn
in another can increase efficiency and possibly save on drying
costs.
It can also relieve some of that sense of urgency for the producer.
The wettest corn can be dried first before it gets hot in the bin
and starts the mold and decay process. Drier corn can be stirred and
aerated to help maintain the integrity of the crop until it gets to
the dryer.
[to top of second column] |
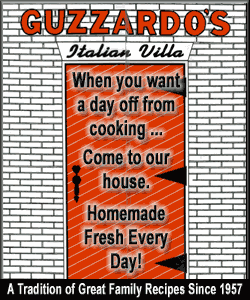
The new monitoring systems can also show the producer in real time
what varieties performed well this year on several levels. While
yield is expected to be high this year, the later it gets into the
season, the greater the possibility for downed corn.
Down corn and fallen ears obviously affect yield. While the dream
come true for a farmer would be a corn that stands well regardless
of the weather conditions, not all hybrids are going to give them
that. Looking at the corn physically in the field, comparing the
yield in bushels and the dryness of the grain, can offer some
insight as to what worked well and what didn’t in this particular
year.
While farmers don’t yet have a crystal ball that tells them what next year will
bring, what they can have is a history of what hybrids performed consistently
well in certain fields under a variety of conditions.
Not everything is determined by the weather or the hybrid. If a field has
trouble spots, the monitoring system will record that. If the same area has a
problem next year, a yield history is in the making. Over time, the monitoring
system which transfers data to the home computer will tell the farmer what he
may be able to expect from a certain field.
If one uses this information coupled with field mapping and soil test mapping,
the producer can create a scientific profile of that field. With such
information, the producer can make smarter choices on tillage practices,
fertilizers, and seed that should be grown there.
Another great innovation in the evolution of the combine is the adjustable
spreader. Everyone knows that crop waste is discharged out the back of the
combine, but how that waste falls on the field is now something that can be
controlled through automated settings inside the combine.
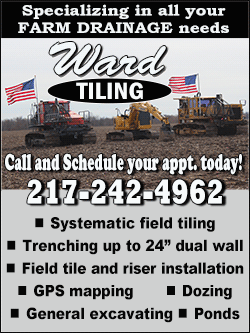
For many, the waste product will become residue in the field. Residue has value
as it can deter soil erosion, or it can be tilled under to help break up
compacted soils and provide some soil nutrient value. With a wet year,
compaction will be an issue and crop residue will have value in the field
looking ahead to 2015.
But, there are some producers, who also have livestock, and as the markets
fluctuate on grains as well as beef and pork, efficient feeding programs could
include baled corn stocks. Today’s spreaders can be adjusted to accommodate
that, with a narrowing of the back fan; corn stalks can be windrowed right out
of the combine and ready to bale. Though wheat is not a large crop in Logan
County, the combines will do the same for those who are looking to bale straw.
Another extremely important innovation is the 'Geo-fence’ feature in the new
combines. Back in the day, leaving the combine in the field five miles from the
house was not a big deal, everyone did it. Today’s machines are huge investments
and as has been described here, chalked full of equipment that some might
consider to be fun little toys to swipe and trade. The Geo-fence is an on-board
security system that can alert the farm house when a piece of equipment is being
moved or messed with in some fashion.
And finally, in spite of all the new gadgets, the first thing any machine
operator should do before firing up that combine is go old-school. Dig out the
operator’s manual and review the to-do list, check out and refresh yourself on
the calibration processes and follow the instructions on maintenance and safety.
Today’s machines are bigger and better than ever, but they are still just as
dangerous when not operated properly as the two row pull-behind corn picker, so
be smart, be safe, and may the bushels be there for you.
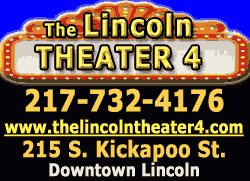
|