The Takata plant there has been confirmed as the source of
defective air bags made in 2001 and 2002 and again around 2012,
according to recall records, automakers and regulators. In 2006, the
factory blew up, driving home for workers and residents the
volatility and risk of the explosive compound at the core of
Takata’s air bags.
Now, the U.S. National Highway Traffic Safety Administration (NHTSA)
has ordered Tokyo-based Takata Corp to submit a wide array of
records, including those pertaining to manufacturing controls at the
Mexican plant, as part of an investigation into why its air bags
have shot shrapnel at drivers in five fatal accidents from Oklahoma
to Malaysia.
All five of the victims - including three in the last 14 months -
were hit by shrapnel from air bags in Honda vehicles. At least
another 160 injury claims involving cars from several automakers
have been reported to NHTSA, according to a Reuters tally.
Interviews with 21 former and current Takata workers and
consultants, along with company presentations and email reviewed by
Reuters reveal the pressure inside the Japanese supplier to ramp up
output and drive down costs for inflators - the mechanism that
triggers air bags to deploy in a fraction of a second after a crash.
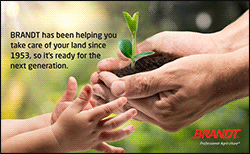
The accounts include the concerns of managers that workers broke
quality rules to boost output. It isn't clear whether the
productivity pressures and quality issues they describe led to
specific accidents. But the portrait they draw suggests that top
executives at the company were not fully aware of what was going on
at the foreign factories that churned out millions of air bags. So
far, the Takata problems have led to the recall of over 16 million
vehicles worldwide.
“We are highly focused on cooperating with NHTSA and the (U.S.)
government investigation,” Takata's U.S. spokesman Alby Berman said
in response to questions sent by email.
The NHTSA administrative order requires Takata to supply documents
and answer questions under oath related to any problems in producing
air bag inflators. The order was prompted in part by an Oct. 17
Reuters report detailing production and quality problems at the
Mexico plant. The company has until Dec. 1 to comply. In addition to
the regulatory probe, Takata faces a criminal investigation by U.S.
prosecutors.The investigations come as the Mexico plant gears up to
make parts needed to replace millions of air bags in the ongoing
vehicle recalls.
'WE’RE SCARED’
On the evening of March 30, 2006 Takata’s Mexican air bag factory
exploded a year into its run as the company’s main inflator
production point. The series of blasts blew out windows on houses a
kilometer away and threw up fireballs as workers and residents fled
to escape injury, witnesses say.
Remarkably, residents and workers say, there were no injuries.
Hundreds of workers inside the factory that evening all managed to
evacuate, some by climbing over a factory fence because a gate had
been mistakenly left shut.
Takata, which accounts for about a fifth of global air bag
production, never announced the exact cause of the 2006 explosion,
workers there at the time said. An official at the fire department,
where Takata has donated trucks, said he had no records from that
time.
Some workers said the blast was fueled by bunkers of ammonium
nitrate stored next to the plant. Takata air bags are inflated using
ammonium nitrate, an explosive propellant that is encased in a
canister to make an inflator.
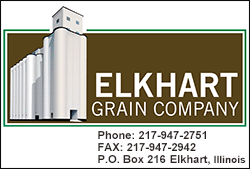 Josefina Vargas lives next door to the Takata factory. She said the
first sign of trouble from the factory was a thin line of smoke
visible from the sidewalk in front of her house. Vargas, 52, who did
not work at Takata, remembers her shock as explosions threw fiery
debris almost to her feet as she sat outside her house. Vargas and
others fled by foot and by car.
“We’re scared,” Vargas told Reuters in recounting the explosion from
her home where she sells tortillas and cookies. “When we hear a
sound now, we think it’s the plant.”
Takata's Berman said the company's safety training had "allowed for
the successful evacuation of thousands of employees within a few
minutes of the discovery of the fire and prevented a possible loss
of life." He said the company had put new safety policies in place
after the accident.
Alejandro Perez, a former Takata facility manager, stayed at work
for four days straight after the accident, taking short breaks to go
home and nap or shower, he said.
The company offered workers who returned and stayed on the job
special incentives, Perez and other workers say. Takata raffled off
televisions, refrigerators and cars, and even held Easter services
at the plant for workers on the job that April 16.
Takata managers were proud of the comeback. They marked the
rebuilding with a commemorative in-house coffee table book with
pictures of the blast, and baseball caps stitched with the exact
date and time of the first explosion. The company took a $21 million
charge as it prepared for an IPO in November of that year.
Within a month, Takata had resumed production, fast enough so that
customers such as Honda Motor Co, Ford Motor Co didn't have to shut
down their own factories due to lack of parts. Rival Autoliv also
stepped up its output to make up for what Takata could not supply,
the companies said at the time.
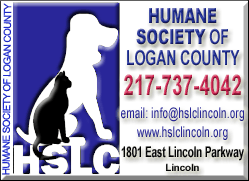
UNRELENTING PRESSURE
But on the ground, the pressure to restart and make up for lost
production was unrelenting, especially from American managers who
had been flown to Mexico, said Perez, the former facility manager.
He was laid off at the plant in 2008. Other workers also said
pressure remained high.
Takata workers said they had to make a quota of inflators -
sometimes more than 200 per hour. “If you didn’t make it, you would
be behind and they wouldn’t pay you a productivity bonus,” said Jose
Sanchez, 42, a former worker who made inflators at Takata from 2004
to 2010.
In 2010 and 2011, the Monclova plant was consistently behind quota
in making a new kind of driver’s-side air bag inflator. In an effort
to crack down, supervisors used security cameras to catch workers on
a line “fooling around,” and apparently engaged in conversation
rather than making inflators, an email circulated to staff that
included still images from a camera shows. Takata's Berman said
security cameras at the plant were there to prevent theft and not
intended to monitor workers.
Around the same time, a worker was also cutting corners by trying to
“rework” or fix defective parts on the inflator assembly line. That
would have made it easier for them to meet output quotas. But Takata
prohibited that practice in order to reduce the chances of bad parts
being shipped to automakers, according to an email. Inflators
identified as defective were supposed to be placed in a separate,
red bin and then examined and repaired if possible by other workers,
according to former workers.
[to top of second column] |
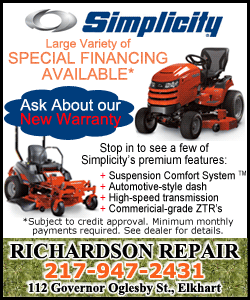
Guillermo Apud, a supervisor at the plant, scolded other employees
about this problem in a May 2011 email reviewed by Reuters. “Rework
on the line is PROHIBITED!!!!” he said. “We can't have
leaders/materials people/operators REWORKING material left and right
without ANY control, this is why we have defect upon defect,” his
email, translated from Spanish, said. "We need to change NOW!"
Apud declined to comment. Berman said Apud was acting to reinforce
company safety guidelines after finding an employee had improperly
reworked an inflator. “The email is an example of the manager
performing his supervisory responsibility and enforcing company
quality controls,” he said. In 2012, Takata workers at the Mexico
plant put the wrong part into inflators being readied for shipment,
according to documents Takata and automakers filed with NHTSA. More
than 350,000 vehicles from three different car makers were later
recalled for that defect. The mistake was possible because parts
bins were kept too close together, the company told regulators in
Japan.
The mistake was not discovered until after a lawsuit was filed over
an October 2013 accident when Brandi Owens, then 25, hit another car
in stop-and-go traffic while driving a new GM Chevrolet Cruze. The
Cruze’s air bag exploded and hit Owens so hard it blinded her in the
left eye, she said in the lawsuit filed in April 2014. Her case
prompted a recall two months later, in June. Owens settled with
Takata and General Motors Co on undisclosed terms in August.
A fatal accident just after that June vehicle recall illustrates the
complexity of the problem facing automakers and safety
investigators. Takata said a defective inflator from its
now-shuttered plant in the U.S. state of Georgia was installed in a
2003 Honda City assembled in Thailand and sold in Malaysia.
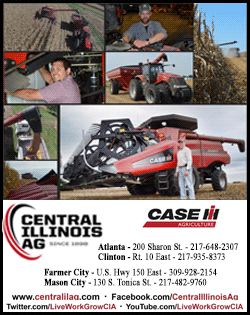 On July 27, Law Suk Leh was driving that car when she hit another
vehicle in the Malaysian town of Sibu on Borneo island. Law, who was
in the final stages of pregnancy, was killed by a “severe puncture
wound” to the neck when she was hit by a metal fragment after the
car's air bag blew apart, Malaysian police said. Honda revealed
details of the death last week in announcing a recall of another
170,000 vehicles to replace their air bags.
BOOMING DEMAND
For Takata, building the factory in Mexico in 2000 would enable it
to help meet booming demand for air bags with cheaper labor,
projections prepared for executives show.
By moving inflator production from two plants in the United States
to Mexico, Takata saved $70 million in labor costs over five years
to 2006, an internal company presentation shows, dropping the labor
cost for making an inflator from $2 to about 75 cents. Takata's
automaker customers benefited: the cost to them fell by more than 20
percent to less than $20 each, according to the presentation.
By spring 2005, Takata’s big bet on the Mexican factory appeared to
be paying off. Workers at the Monclova plant, as it was known in the
company, posed for a commemorative photo, raising both hands in the
air in a banzai salute.
Soon afterward, Takata closed its factory in La Grange, Georgia,
southwest of Atlanta. Takata had been reducing inflator production
there and at a second U.S. plant in remote Moses Lake, Washington
for four years, records show.
Worker morale had suffered at the plant in Moses Lake, built on the
site of a former U.S. military base, workers there told Reuters. By
2000, a new management team prioritized meeting output quotas and
enforced overtime as demand for U.S. cars and SUVs soared, former
workers say. “We just burned people out,” said one former worker,
who like others asked not to be named. In 2002, the plant laid off
100 workers and sent more production to Mexico, media reports at the
time said.
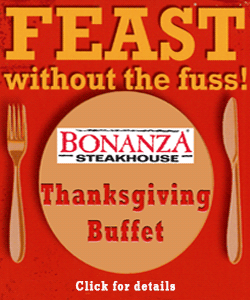
A series of mistakes by workers in handling ammonium nitrate at the
La Grange, Georgia and Mexico plants between 2000 and 2002 left the
explosive compound exposed to dangerous levels of humidity, Takata
told regulators in the United States and Japan.
Takata says inflators could be susceptible to rupture if exposed to
moisture or extreme humidity. The defect in Law's airbag in the
Malaysian accident was caused by humid conditions at the Georgia
plant, Takata and Honda said.
It is unclear how much Takata’s headquarters in Tokyo knew about the
problems at its inflator plants. Takata did not dispatch permanent
staff from headquarters to the Mexican plant as it ramped up output,
workers say.
A Takata safety auditor dispatched from the United States inspected
the Mexican inflator plant in May 2011 and found problems in
handling the volatile ammonium nitrate. His audit report, seen by
Reuters, faulted the plant for not closing bags of the compound
tightly enough and for storing scrapped or contaminated propellant
near good material, risking mix-ups. He said in his report he would
not send the audit to Takata's headquarters in Tokyo.
Shigehisa Takada, the grandson of the founder, now chairman and
chief executive, has said the company made a mistake by allowing too
much autonomy to its local managers in North America during a period
of rapid growth. Takata acquired at least six companies in the
United States and Germany between 1989 and 2012.
“Back then, the U.S. markets were expanding very rapidly, and we
could not see everything that was happening there,” according to a
recording of Takada's speech to a closed shareholders meeting in
June. It was his most recent public appearance.
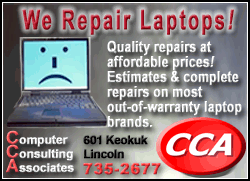 (1 US dollar = 116.5800 Japanese yen)
(Additional reporting by Yoko Kubota in Tokyo, Gabriela Lopez in
Ciudad Frontera and Paul Lienert in Detroit.; Writing by Kevin
Krolicki, editing by Bill Tarrant and Peter Hirschberg.)
[© 2014 Thomson Reuters. All rights
reserved.] Copyright 2014 Reuters. All rights reserved. This material may not be published,
broadcast, rewritten or redistributed. |