Companies like Whirlpool and Caterpillar are making costly
additions to their otherwise sinewy supply chains to compensate for
aging U.S. roads that are too potholed and congested for "just in
time" delivery.
Some opt to keep more trucks and inventory on the road. Others are
leasing huge "just in case" warehouses and guarded parking lots on
the edges of big cities. All that activity raises costs, which are
expected to increase even more if roads are allowed to deteriorate
further and an improving economy boosts traffic.
Whirlpool, for instance, has set up a network of secure drop lots
outside Chicago, Milwaukee and Minneapolis. A washing machine that
used to go from regional distribution center to local distribution
center to customer in one day now sits overnight in a parking lot.
It "adds an extra day of lead time, which means extra inventory,"
said Whirlpool Corp logistics chief Michelle VanderMeer.
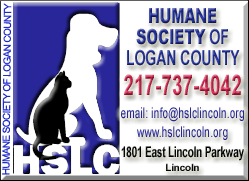 Then there are the parking lots and the guards. “That’s real
physical infrastructure and security that we have to pay for," she
said. "We’d rather be investing our money elsewhere," she added,
declining to estimate Whirlpool's expenses.
Overall, U.S. companies face billions of dollars in costs due to the
limitations of the creaking, overcrowded transportation network,
which earned a D+ grade in the most recent report card from the
American Society of Civil Engineers (ASCE).
The Texas A&M Transportation Institute estimates that road
congestion alone costs shippers $27 billion a year – and that is
only the value of wasted driver time and extra fuel.
“What it doesn’t take into account is the cost of all the extra
trucks and all the extra inventory in transit that manufacturers
have to roll out to make sure their deliveries get there on time,”
said Bill Eisele, a senior research engineer at Texas A&M.
Manufacturers are lobbying Congress to approve new repair funds next
year, with low expectations. The Highway Trust Fund, which finances
road and bridge repairs, narrowly avoided insolvency this summer
when lawmakers approved funding through May.
The current gas tax which funds repairs raises $40 billion annually
and has not been raised in two decades. There is little appetite in
Washington, D.C to raise the gas tax to bring in the $170 billion
the Federal Highway Administration estimates is needed annually to
improve roads.
So manufacturers improvise.
Commercial real estate advisers at Colliers International, Jones
Lang LaSalle and CoStar report a proliferation of “just-in-case”
warehouses popping up in heavily congested urban areas.
The Polar Vortex which froze much of the nation last winter and
2012's Hurricane Sandy in the Northeast were disasters for shippers
and catalyzed the move. The trend is now being pushed by
expectations that an improving economy will further crowd roads and
raise costs, they said.
[to top of second column] |
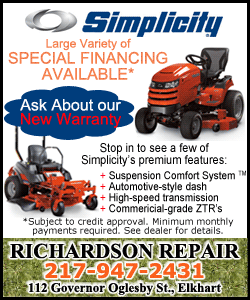
Outside Chicago, Panasonic Corp, Ingram Micro and Owens & Minor have
all leased spaces in recent years to help take congestion-related
variability out of their supply chains, according to CoStar. An
item which passes through two warehouses requires about 50 percent
more inventory than an item which passes through one, said Rene
Circ, CoStar's director of industrial research.
"It either costs the companies in the form of lower margins and
profits or customers in the form of higher prices," he said.
As the world’s largest maker of big earth-moving equipment,
Caterpillar is also one of the world’s largest shippers by weight,
moving 12 billion pounds of machines, engines and parts globally
each year, much of that out of its plants in the
central and southern United States.
Many of those machines are exported. To get them to ports on the
east and west coasts, Caterpillar often breaks some of its heaviest
machines into parts and then re-assemble them on the dock before
loading them onto ships for export.
Crazy? Not according to Ed O'Neil, the company's logistics chief. It
turns out that all that extra work actually costs Caterpillar less
than obtaining the state-issued heavy-load permits required to move
the machines fully assembled over highways whose capacity has been
cut in recent years because of a lack of upkeep.
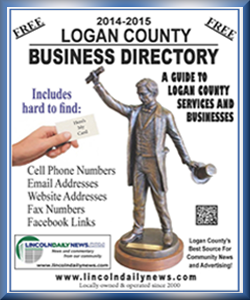
“It’s a better business decision to spend the money to tear
it apart and then to put it back together than it is to try to
send it as one piece," O'Neil says.
(Reporting by James B. Kelleher in Chicago, editing by Peter
Henderson)
[© 2014 Thomson Reuters. All rights
reserved.] Copyright 2014 Reuters. All rights reserved. This material may not be published,
broadcast, rewritten or redistributed. |