Chelten House Products makes private-label sauces and dressings for
high-end grocers such as Whole Foods, Trader Joe's and Kroger, and
has doubled its workforce to 300 over the past five years to keep up
with a booming organic food market.
Now it is struggling to hire not just skilled mechanics or
electricians but even workers who handle the jars rolling down its
conveyer belts. Chelten CEO Steve Dabrow says factory work is
becoming a harder sell with unemployment down at a seven-year low of
5.3 percent. "You're not sitting down, you're standing on your feet
all day, you're not taking breaks, and bottles are flying down the
line," he said.
The Bridgeport, New Jersey, company, which hired 60 people just last
year, is not bidding up wages much for anyone save those with very
specialist skills because, for now at least, it still manages to
fill the vacancies. It has made some strategic capital investments,
such as in a more automated new plant in Las Vegas in 2013, but has
more recently focused on expanding by taking on additional workers.
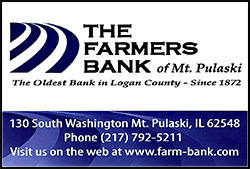
Like other U.S. manufacturers for whom the 2007-2009 recession is
fast-fading, this company's story of brisk hiring, limited wage
hikes, and some capital investment helps illustrate why the
otherwise mostly rosy U.S. labor market is marred by low wage growth
and sinking productivity.
Interviews with several heads of small and midsize companies,
together with results from employer surveys and data on labor costs,
indicate that while companies are prepared to hire more workers,
they do not feel the need to raise wages significantly or have the
confidence in the economy to make big capital investments. This is
good for the job numbers but it is restraining productivity and
economic growth.
Dabrow and managers at other U.S. manufacturing companies say they
often need to bring on workers who lack the experience or dedication
of those hired in 2009, when U.S. unemployment peaked at 10 percent.
That means a lot of on-the-job training and staff turnover that may
keep U.S. productivity, or output per worker hour, from rebounding
quickly from its first back-to-back quarterly drop since 2006.
(Graphics: http://link.reuters.com/cuj32w http://link.reuters.com/xyb62w)
SHY ABOUT SPENDING
How soon and how strongly wages and productivity rebound will
influence Americans' standard of living, and have a big effect on
the inflation rate and economic growth. As a result, it will help
the Fed determine whether to raise interest rates for the first time
in nine years in September or later.
Fed officials are assuming there will be a rebound in productivity
through innovation or investment in labor-saving technology like
robotics, and that this will boost economic growth to around 2.5
percent next year. They also don't expect the jobless rate to fall
much further through the end of this year.
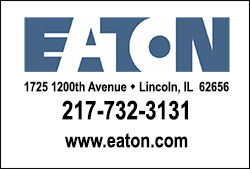
But if productivity remains weak it could push the inflation rate
higher and lead to a more aggressive policy tightening in the months
and years to come. "Overall productivity has been disappointing,"
Boston Fed President Eric Rosengren told Reuters in a recent
interview.
Manufacturing, where productivity fell by 1 percent in the first
quarter compared with 3.1 percent economy-wide, should be at the
forefront of the expected investment-driven bounce. But in a
closely-watched proxy for investment, shipments from American
factories of civilian capital goods other than airplanes rose only
0.6 percent in June from a year earlier, suggesting businesses are
still shy about spending on anything beyond hiring.
While many industrial giants like Caterpillar have been squeezed by
the strong dollar and weak overseas markets, triggering job cuts,
smaller U.S. firms are in better shape. With less overseas exposure
and accounting for 60 percent of job gains since the recession, they
are planning to spend and hire more, according to a June survey by
the National Federation of Independent Business.
[to top of second column] |
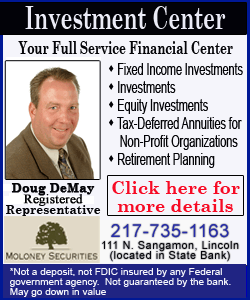
For example, Gray Construction CEO Stephen Gray hired 67 people over
the past six months to bring the workforce of his Lexington,
Kentucky-based company up to 375. But he said wage increases were
reserved only for the highly skilled workers, who made up about a
third of new hires.
The company designs, engineers and manages building of factories for
the likes of Toyota Motor Corp and Caterpillar, and Gray sees a
"green light" for manufacturing until at least 2018 thanks to
resilient U.S. consumption and, despite recent weakness,
productivity that still tops that of European rivals.
But that doesn't mean it is spending heavily on new equipment.
"When we roll the dice it's on people," Gray said. "We're not buying
robotics, we're not buying big software systems."
WAGE GROWTH TEPID
After some tentative gains in recent months, U.S. wages were steady
in June, with the average inflation-adjusted pay of manufacturing
production workers, at $8.49 an hour, the same as it was in 2007,
and little above the $7.25 an hour federal minimum wage.
A measure of employment costs, which also includes health and
pension insurance, also stalled in the second quarter, though the
weakness was not expected to last, according to economists and
policymakers.
Tepid wage growth helps explain the productivity slump, says Mark
Zandi, chief economist at Moody's Analytics. "It's been cheaper for
companies to expand by hiring people rather than investing," he
said. But once wages start rising, investment and productivity
should pick up, he added.
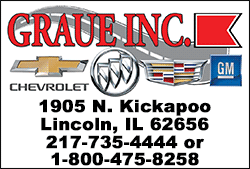
D'Addario, which makes guitar strings and other musical instrument
accessories, reflects the sober views that many manufacturers' have
about the economy.
The strong dollar forced it to cut prices in its export markets in
Europe, Brazil and Australia. Rather than scale-back, the
Farmingdale, New York-based company decided to cut imports of
materials to save on shipping costs and to ramp up in-house local
production, its president John D'Addario III said.
Faced with growing staff turnover, the company has chosen to lure
new workers by stressing the benefits it offers rather than raising
wages that start at $9.75 an hour.
Some executives simply doubt the world's largest economy can do much
better than the 2.3 percent annualized growth it recorded in the
second quarter.
For the 350 employees of Millerbernd Manufacturing in Winsted,
Minnesota, which makes heavy metal rings, cylinders and
street-lighting poles, wages in step with inflation are the order of
the day, says chief operating officer Rob Tracy.
"We're operating on the assumption that this flat economy is the new
normal," he said.
(Reporting by Jonathan Spicer; Additional reporting by Meredith
Davis in Chicago and Jason Lange in Washington; Editing by Tomasz
Janowski, David Chance and Martin Howell)
[© 2015 Thomson Reuters. All rights
reserved.] Copyright 2015 Reuters. All rights reserved. This material may not be published,
broadcast, rewritten or redistributed.
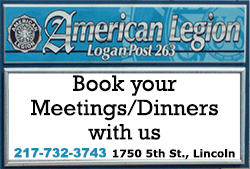 |