Australian researchers unveil world's
first 3D printed jet engine
Send a link to a friend
[February 26, 2015]
By Jane Wardell
SYDNEY (Reuters) - Australian researchers
unveiled the world's first 3D-printed jet engine on Thursday, a
manufacturing breakthrough that could lead to cheaper, lighter and more
fuel-efficient jets.
|
Engineers at Monash University and its commercial arm are making
top-secret prototypes for Boeing Co, Airbus Group NV, Raytheon Co
and Safran SA in a development that could be the savior of
Australia's struggling manufacturing sector.
"This will allow aerospace companies to compress their development
cycles because we are making these prototype engines three or four
times faster than normal," said Simon Marriott, chief executive of
Amaero Engineering, the private company set up by Monash to
commercialize the product.
Marriott said Amaero plans to have printed engine components in
flight tests within the next 12 months and certified for commercial
use within the next two to three years.
Australia has the potential to corner the market. It has one of only
three of the necessary large-format 3D metal printers in the world -
France and Germany have the other two - and is the only place that
makes the materials for use in the machine.
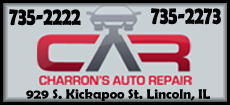 It is also the world leader in terms of intellectual property (IP)
regarding 3D printing for manufacturing.
"We have personnel that have 10 years experience on this equipment
and that gives us a huge advantage," Marriott told Reuters by phone
from the Avalon Airshow outside Melbourne.
3D printing makes products by layering material until a
three-dimensional object is created. Automotive and aerospace
companies use it for producing prototypes as well as creating
specialized tools, moldings and some end-use parts.
[to top of second column] |
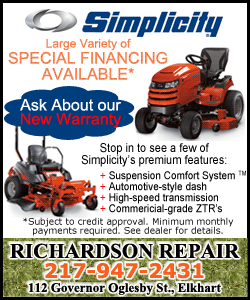
Marriott declined to comment in detail on Amaero's contracts with
companies, including Boeing and Airbus, citing commercial
confidentiality. Those contracts are expected to pay in part for the
building of further large format printers, at a cost of around A$3.5
million ($2.75 million) each, to ramp up production of jet engine
components.
3D printing can cut production times for components from three
months to just six days.
Ian Smith, Monash University's vice-provost for research, said it
was very different to the melting, molding and carving of the past.
"This way we can very quickly get a final product, so the advantages
of this technology are, firstly, for rapid prototyping and making a
large number of prototypes quickly," Smith said. "Secondly, for
being able to make bespoke parts that you wouldn't be able to with
classic engineering technologies."
(Editing by Paul Tait)
[© 2015 Thomson Reuters. All rights
reserved.]
Copyright 2015 Reuters. All rights reserved. This material may not be published,
broadcast, rewritten or redistributed.
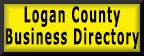 |