Before the mine even opened, Ed was employed by the construction
company that was hired to drill three vertical shafts that were
necessary to access the coal seam that was discovered three-hundred
below the surface just south of Elkhart. Each shaft has a specific
purpose. An intake shaft was necessary to bring the miners to the
underground seam and to bring in equipment. A second material shaft
was constructed to bring the mined coal to the surface. And, finally
a third shaft called an exhaust shaft pulled air out of the mine.
This shaft was necessary to insure that fresh air was always
available to the personnel three-hundred feet below the surface.
Before construction of the three shafts could begin, hundreds of
small bore holes were drilled on a two-foot grid to locate the
thickest part of the coal seam. Once the optimum location of the
coal depth was located, 300 feet below the surface of the farm
ground south of Elkhart, the three shafts could be sited to provide
maximum access to the coal. Now, the real work was ready to begin,
the drilling of the three shafts down to the coal seam, each with a
thirty-foot diameter.
Not so fast! “The bore holes discovered a unique situation that was
going to make the drilling of the three shafts difficult,” said
Block. Instead of a shallow depth of soft surface soil followed by
bed rock down to 300 feet, the bore holes uncovered the fact that
the soft surface soil continued to a depth of thirty feet followed
by a few feet of bed rock which in turn was followed by more soft
soil. This alternating geological formation continued to the final
depth. Most geology would be a few feet of soft surface soil
followed by bedrock to the required depth.
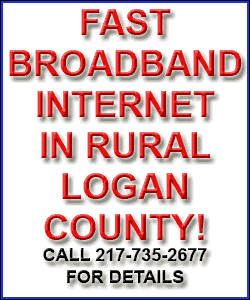 The bedrock is necessary to encase the shafts as they are drilled,
providing a hard structure around the shafts. Once this headache was
uncovered, another method of drilling the three access shafts had to
be used. A solid structure would have to be placed around the shafts
to hold them up.
“The engineers came up with a unique way to replace the non-existent
bedrock,” said Ed Block. Small bore holes were drilled around the
thirty foot diameter area of the three access shafts down to the
final depth and filled with Freon, the essential substance that
makes air conditioners function. In essence, the Freon injection
froze the ground solid within the diameter of the shaft, thus
creating artificial bedrock.
“Once the ground was frozen, a series of four foot deep holes were
drilled within the area of the vertical shaft, stuffed with
dynamite, and exploded,” said Block. Then a small digging device
called a mucking machine was lowered into the hole and used to dig
out the loose material and deposit it into a bucket that was hauled
out.
Then the mucking machine was removed, another series of holes was
bored and blown up. The mucking machine was again lowered into the
hole to clear it of the next layer of loose material. This went on
down to the final depth of 300 feet.
Once the three shafts were completed, which involved pouring
concrete continuously from 300 feet to the surface to form walls,
they had to be connected.
“After the shafts were connected and tested for stability, we were
able to begin the real work of coal mining. The Elkhart mine is a
room and pillar mine,” he said. That means that an area like the
street pattern of a town was mined. Coal was mined from the
“streets” and shipped to the surface while the blocks of the “town”
were left in place to hold up the mine.
[to top of second column] |
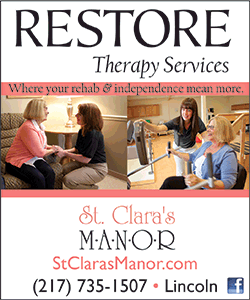
The mining operation found that the most beneficial direction for mining was
south. Mining north and west found the coal seam disappearing quickly. To the
south, coal remained in the original thickness. Some mining was done under
Elkhart Hill, but that direction was soon abandoned. As with most room and
pillar mines, the area of the “streets” will eventually collapse. It is
estimated that Elkhart Hill will drop five to six feet at some point. This area
had to be treated with a special technique so that the Hill would fall evenly.
“Elkhart Hill is so big that when the mine tunnels finally do collapse, it will
not be noticeable,” said Block.
Ed noted that construction of the three vertical shafts uncovered some
interesting geology and archeology. In addition to the lack of bedrock, three
areas of sand were found under the farmland. The first area of fine white sand
was found at a depth of 120 feet and was one foot thick. At a depth of 180 feet,
another area of sand was located that was three feet thick. A final layer of
fine white sand was found at a depth of 195 feet that was ten feet thick.
Ed queried his audience as to where sand is usually found. “We had uncovered the
shores of three different inland oceans that had existed in central Illinois
long ago,” he said.
The drilling also uncovered the petrified remains of prehistoric animals,
shells, and plants. “It was thrilling to uncover these remnants of the ancient
planet. I found a seed pod that was two feet long, and a three-foot long
reptile. Unfortunately these fossils crumbled to nothing when we tried to
recover them,” he said.
It was also determined that the coal seam at Elkhart is the same one that
underlies the area near Carmi, Illinois. The Elkhart seam is 300 feet deep while
the seam at Carmi, the same seam, is 600 feet deep. Carmi is approximately 150
miles southeast of Elkhart.
Ed Block was hired at the Elkhart mine after teaching school in Broadwell for
several years. “Mining paid better than teaching,” he said with a grin.
After beginning his job as safety and training officer at the mine, Block became
a miner. He worked almost fifteen years underground at the mine. As safe as the
Elkhart mine was, mining is still a dangerous job. “One week, I was injured
three times requiring three trips to the hospital to be checked out. At that
point, my family urged me to find a safer career,” he said. He agreed and moved
on to a job away from coal mining that did not require going underground. Now
retired, he is a substitute teacher.
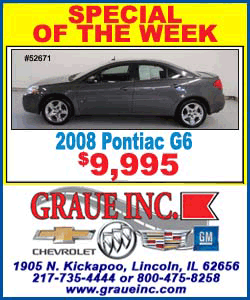
The Logan County Genealogical and Historical Society monthly meeting is the
third Monday of each month at 6:30 p.m. at the research facility at 114 North
Chicago Street in Lincoln. There is always an interesting presentation, and it
is open to the public. Contact the LCGHS at (217) 732-3200.
[Curt Fox] |