That could soon change as cheaper, faster and more flexible robots
mean manufacturing - including producing fiddly footwear - could be
brought closer to consumers in high-wage countries like Germany,
speeding up delivery and slashing freight costs in what some call a
fourth industrial revolution.
Adidas is working with the German government, academics and robotics
firms on new technologies it hopes will trigger a significant a
shift in the footwear industry as the move led by its arch rival
Nike to produce in Asia decades ago.
The project is part of a broader drive by Adidas to catch up with
Nike, which has extended its lead as the world's biggest sportswear
firm in recent years with innovative products such as its "Flyknit"
shoes made out of machine-knitted fiber.
"We will bring production back to where the main markets are,"
Adidas Chief Executive Herbert Hainer said in March. "We will be the
leader and the first mover there."
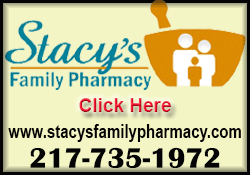
Adidas hopes to be able to produce a custom-made running shoe from
scratch in a store in Berlin by next year, using a stitching machine
and a foamer to make the sole.
Nike, which has long faced criticism for using Asian sweat shops to
produce its pricey footwear, is also investing heavily in new
manufacturing methods. But it has not yet put a date on when it
expects that to result in more U.S.-based production.
JOBS AT RISK
Key to moving footwear manufacturing closer to Western markets are
technologies which cut the need for workers to piece together shoes.
A machine can now "knit" an upper like a sock, robots can already
complete more of the final assembly of the shoe, while 3-D printing
could soon allow the production of a customized sole.
That could threaten millions of jobs in the footwear industry in
countries like China, Brazil and Vietnam, but potentially create new
positions elsewhere, albeit for more highly skilled laborers working
alongside robots.
Robots, now used mainly in auto production, could soon cut labor
costs by 18 percent or more by 2025 in other sectors, the Boston
Consulting Group (BCG) predicts.
The new technology is being closely guarded: photographers were not
invited to an investor presentation at the Adidas innovation center,
where it demonstrated a robot that could stick its trademark three
stripes to a running shoe.
Nike, for its part, tried to stop Adidas producing a knitted shoe
that it said violated patents for the "Flyknit" technology it
launched in 2012. However, a German court ultimately allowed Adidas
to resume production of its "Primeknit" shoes.
Nike says it can make "Flyknit" shoes with half the labor input of a
typical "cut-and-sew" shoe as it has 80 percent fewer components,
also resulting in 70 percent less waste as it no longer needs to cut
pieces from a pattern and discard the rest.
Nike co-founder Philip Knight shook up the sporting goods industry
that Adidas has dominated until the 1970s after putting into
practice his thesis paper arguing that sneakers from lower-cost
Japan could compete with pricier German-made versions.
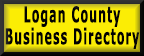
Today, Asia produces 87 percent of all footwear, with China by far
the biggest manufacturer, followed by India, Brazil and Vietnam,
according to APICCAPS, the association of Portuguese footwear
manufacturers that compiles global industry figures.
[to top of second column] |
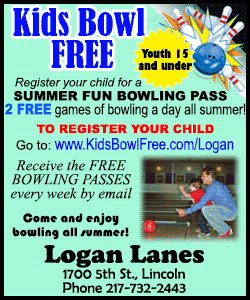
INCREASING SPEED TO BOOST MARGINS
Nike and Adidas each rely on more than 1 million workers in contract
factories worldwide to make their shoes.
While the need for speed is one motivating factor, rising wage
costs, particularly in China, are also driving the shift.
"That element is going up dramatically," said Glenn Bennett, head of
global operations for Adidas who leads the project aimed at getting
products to shoppers faster than the six weeks needed for shipments
to arrive from Asia.
Adidas is working with companies like automotive supplier Johnson
Controls, robotics experts Manz and knitting machine maker Stoll on
new processes as it targets prototype in-store manufacturing by next
year.
Adidas says more local manufacturing should leave it with less
surplus stock it has to discount, helping to lift its operating
margin above 10 percent from 6.6 percent in 2014, still behind the
13 percent Nike recorded last year.
Nike, which saw sales in North America dampened earlier this year by
delays to deliveries from Asia due to labor disruption at ports on
the U.S. West Coast, is unlikely to allow its German rival to get
much of a headstart on localized production.
During a visit by U.S. President Barack Obama to Nike headquarters
last month, the firm promised to create 10,000 jobs in the United
States in the next decade by producing more in its home market if a
trade deal with Asian countries is approved.
"We are putting a lot of money and a lot of resources against how
our supply chain evolves to increase speed and make sure we deliver
to consumers as quickly and innovatively as we can," Trevor Edwards,
Nike brand president, said in March.
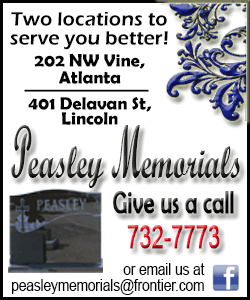
Beyond knitting and 3-D printing, other innovations helping to speed
up production include bonding and gluing technologies to fuse
together fabrics as well as waterless dyeing which allows pigments
to penetrate textiles more quickly.
Yves-Simon Gloy, an expert from the Institute for Textile Technology
at Aachen University who is collaborating with Adidas and sees the
dawning of a fourth industrial revolution due to the emergence of
"cyber physical systems", machines equipped with sensors, cameras
and motors that can be adjusted using the Internet in real time.
But Bennett and Gloy do not expect these smart machines to
completely usurp human workers.
"The breakthrough will probably happen in finishing the product
close to the consumer," said Bennett. "Not moving the whole of the
operation".
(Editing by Anna Willard)
[© 2015 Thomson Reuters. All rights
reserved.]
Copyright 2015 Reuters. All rights reserved. This material may not be published,
broadcast, rewritten or redistributed. |