Cheaper, greener, route to bioplastic
Send a link to a friend
[February 15, 2016]
By Jim Drury
Polylactic acid (PLA) plastic is an
increasingly common, environmentally friendly, alternative to
conventional petrochemical-based mass plastics. But it's a costly
process.
|
Researchers at the University of Leuven's Centre for Surface
Chemistry and Catalysis have published research in the journal
Science that suggests a new method of simplifying the PLA production
process and making it waste-free.
According to lead researcher Michiel Dusselier: "Instead of (the
current) two-step process currently, it's a one-step process. Our
process runs about 100 degrees centigrade lower in temperature and
our productivities, which is kind of how much product can you make
per volume of reactor per hour are much higher and our product is
also much cleaner, so we don't make side products, for instance,
caused by racemisation or other side reactions because we work at a
lower temperature."
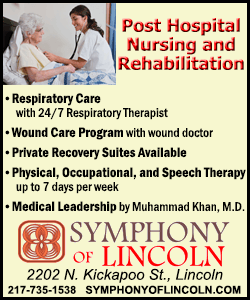 PLA is derived from renewable resources, including the sugar in
maize and sugarcane. Fermentation turns the sugar into lactic acid,
which is a building block for polylactic acid. The production
process for PLA is expensive because of the number of intermediary
steps, which Dusselier's team says it has eliminated. In traditional
PLA production lactic acid is fed into a reactor and converted into
a type of pre-plastic, low quality, material under high temperature
and in a vacuum. The pre-product is subsequently broken down into
building blocks for PLA. These intermediary steps also require
metals and produce waste.
"Our process is based on condensation reaction in which we will
contact lactic acid with a zeolite and zeolites are famous catalysts
from refinery and petrochemical industry, and these catalysts are
micro porous materials - sort of nano sponges - so they have a huge
internal surfaces and they also have limited space inside their
voids, so it's kind of a reactive sponge," explained Dusselier.
PLA will degrade after a few years in particular environments, while
it is also industrially compostable and recyclable. It's
biocompatible, so suitable for medical use, and is also one of the
few plastics suitable for 3D printing.
[to top of second column] |
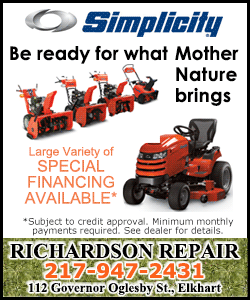
Dusselier says the Leuven process has a selectivity (efficiency) of
85 percent, compared to between 60-70 percent for other PLA
alternatives, and is far more productive in terms of how much
product can be made per volume of reactor. He told Reuters the
remaining side products of traditional PLA processes is waste,
whereas the new method could recycle the remaining 15 percent by
extraction and put back into the reactor, eventually providing a
zero waste process.
Supervising professor Bert Sels expects the new patented method to
be an industrial game-changer. "The impact, I think, will be very
great in the sense that we now have a very competitive process,
where there is a monopoly at the moment," said Sels. "I think there
will now be much more players in the market giving you the product
at much lower prices and I think this will maybe really be the start
of the PLA into the bio-plastic business."
The patent was recently sold to a petrochemical company which plans
to apply the production process on an industrial scale.
"The invention was actually done within the university itself, but
we had an agreement now with a petrochemical company that sold the
patent and is now trying to upscale the process to see whether or
not this is commercially feasible," said Sels.
The Leuven team says that PLA will never fully replace
petroleum-based plastics because objects such as toilet drain pipes
are not meant to be biodegradable. But they insist that there is
market for PLA and that by making it cheaper and greener they can
help the global economy and reduce pollution.
[© 2016 Thomson Reuters. All rights
reserved.]
Copyright 2016 Reuters. All rights reserved. This material may not be published,
broadcast, rewritten or redistributed.
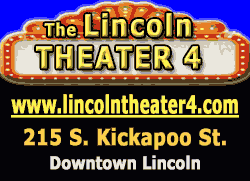 |