The award is part of a larger drive by the U.S. military to end
its reliance on Russian-built RD-180 rocket engines now used on the
Atlas 5 rocket built by United Launch Alliance, a joint venture of
Lockheed Martin Corp and Boeing Co.
The Air Force plans to award additional, larger contracts for
U.S.-developed propulsion systems later this year.
Aerojet said it would draw upon its extensive experience with 3-D
printing, or additive manufacturing, to draw up the standards that
would be used to qualify 3-D printed rocket engine components for
flight.
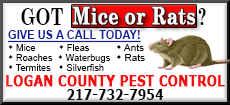
Aerojet is developing its AR1 engine as an alternative to the RD-180
engine. New rocket engine designs like the AR1 are increasingly
using 3-D printing technology because it reduces the amount of time
and money required for the engines.
The use of additive manufacturing technology reduces the cost to
produce components, shortens build times and provides flexibility to
engineers to design components that were once impossible to build
using traditional manufacturing techniques.
The contract calls for Aerojet to define the rigorous engineering
and inspection processes to be followed when producing and testing
3-D printed components to ensure they meet the stringent
requirements of aerospace systems.
[to top of second column] |
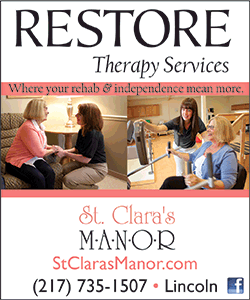
In 2014, Aerojet successfully tested an engine made entirely with
additive manufacturing that had a thrust of 5,000 pounds. A year
later, it used additive manufacturing to replicate the injector of
the gas generator used on the Apollo-era F-1 rocket engine to
demonstrate that a proven design can be built at a competitive cost
without sacrificing performance.
(Reporting by Andrea Shalal; Editing by Kenneth Maxwell)
[© 2016 Thomson Reuters. All rights
reserved.]
Copyright 2016 Reuters. All rights reserved. This material may not be published,
broadcast, rewritten or redistributed.
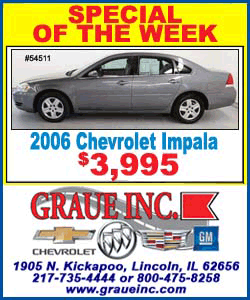 |