Grading, sorting, and processing is slow going. Add to that poor
storage and packaging, inefficient handling and transportation,
and other issues. As a result, post-harvest losses, of
especially perishable products, can reach 40 to 50 percent.
A University of Illinois researcher, who is originally from
Bangladesh, is working to develop inexpensive technologies to
help mango growers in his country reduce the time and tedium in
at least one aspect of post-harvest processing—sorting and
grading.
“There aren’t any computer-based technologies in Bangladesh.
Mangoes are hand-picked from the trees and brought by truck to
the plant,” says Md Abdul Momin who led the research. “The
post-harvest process includes picking up each piece of fruit,
weighing it, and sorting it for quality, such as disease or
blemishes, and size. A mango weighing 300 grams goes in this
pile, 200 gram fruit goes in that pile over there.”
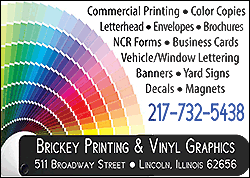
Momin says grading the produce is important as it ensures
high-value products that can be sold at premium prices. There is
a critical need to quickly, accurately, and efficiently assess
agricultural products without the use of human labor.
“Automatic grading and sorting systems that use machine vision
to determine size, shape, color, ripeness, weight, bruising,
disease, rot, etc., are already being used in many countries,”
Momin says. “When I began working with image processing, I
thought it might be something that I could adapt to help make
mango production in Bangladesh more efficient.”
Momin worked with a student and a mango farm manager. The goal
was to develop something inexpensive that could help sort and
grade mangoes, particularly during the peak season in the summer
when Bangladesh is very hot, labor is scarce, and the volume of
harvested fruit becomes overwhelming.
“We used a camera for about $400, a lamp for $50, and tin plate
to create a simple way to collect images,” Momin says. “We
designed the system using parts that aren’t fancy or expensive.
You can even use a web camera that costs about $50 to $100.”
The mangoes are first weighed. Then the camera and light box are
used to determine its area.
[to top of second column] |
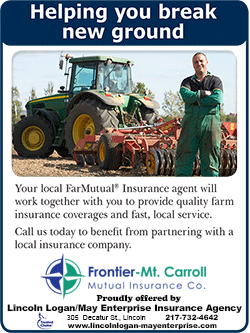
“The camera takes an image showing that the mango is
30,000 pixels so it belongs in the grade A category with the
highest-quality, 300-gram mangoes. Using this technology, we can
separate the harvest into large, medium, and small size mangoes,”
Momin says.
According to Momin, there is also a consumer
preference for roundness. “If they don’t like the shape of the
mango, they don’t want to buy it. So we used another parameter
called roundness. For this technology, the shape parameter does not
translate well to a weight, so that’s an aspect that we need to do
further work on.”
In this initial phase, the imaging is done in a box.
“When scaled up to a system large enough to operate in the
processing plant, it will need to incorporate a moving conveyor belt
or some other method to transport the fruit through the imaging
area,” says Tony Grift who is a co-author on the research paper.
Momin adds that in Bangladesh, there are banana, tomato and potato
crops. And, although this particular research was done on mango, it
can be adapted to other fruits and vegetable crops.
The study, “Geometry-based mas grading of mango fruits using image
processing,” is published in Information Processing in Agriculture.
The research was conducted by Md Abdul Momin, M.T. Rahman, M.S.
Sultana, C. Igathinathane, A.T.M. Ziauddin, and Tony Grift.
This work has been partially supported by The World Academy of
Sciences (Ref.: 13-311 RG/ITC/AS_C); and MoICT, Bangladesh (code:
3-0001-2801-5965).
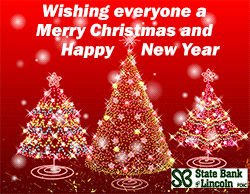
Md Abdul Momin is postdoctoral research associate in the Institute
for Genomic Biology at U of I. Tony Grift is an associate professor
in the Department of Agricultural and Biological Engineering in the
College of Agricultural, Consumer and Environmental Sciences at the
University of Illinois.
[Debra Levey Larson
University of Illinois
College of Agricultural, Consumer and Environmental Sciences] |