How two cutting edge U.S. nuclear
projects bankrupted Westinghouse
Send a link to a friend
[May 02, 2017]
By Tom Hals and Emily Flitter
WILMINGTON, Del./NEW YORK (Reuters) - In
2012, construction of a Georgia nuclear power plant stalled for eight
months as engineers waited for the right signatures and paperwork needed
to ship a section of the plant from a factory hundreds of miles away.
The delay, which a nuclear specialist monitoring the construction said
was longer than the time required to make the section, was emblematic of
the problems that plagued Westinghouse Electric Co as it tried an
ambitious new approach to building nuclear power plants.
The approach - building pre-fabricated sections of the plants before
sending them to the construction sites for assembly - was supposed to
revolutionize the industry by making it cheaper and safer to build
nuclear plants.
But Westinghouse miscalculated the time it would take, and the possible
pitfalls involved, in rolling out its innovative AP1000 nuclear plants,
according to a close examination by Reuters of the projects.
Those problems have led to an estimated $13 billion in cost overruns and
left in doubt the future of the two plants, the one in Georgia and
another in South Carolina.
Overwhelmed by the costs of construction, Westinghouse filed for
bankruptcy on March 29, while its corporate parent, Japan's Toshiba
Corp, is close to financial ruin [L3N1HI4SD]. It has said that controls
at Westinghouse were "insufficient."
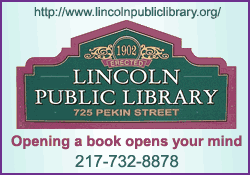
The miscalculations underscore the difficulties facing a global industry
that aims to build about 160 reactors and is expected to generate around
$740 billion in sales of equipment in services in the coming decade,
according to nuclear industry trade groups.
The sector's problems extend well beyond Westinghouse. France's Areva is
being restructured, in part due to delays and huge cost overruns at a
nuclear plant the company is building in Finland.
Even though Westinghouse's approach of pre-fabricated plants was
untested, the company offered aggressive estimates of the cost and time
it would take to build its AP1000 plants in order to win future business
from U.S. utility companies. It also misjudged regulatory hurdles and
used a construction company that lacked experience with the rigor and
demands of nuclear work, according to state and federal regulators'
reports, bankruptcy filings and interviews with current and former
employees.
"Fundamentally, it was an experimental project but they were under
pressure to show it could be a commercially viable project, so they
grossly underestimated the time and the cost and the difficulty," said
Edwin Lyman, a senior scientist at the Union of Concerned Scientists,
who has written and testified about the AP1000 design.
Westinghouse spokeswoman Sarah Cassella said the company is "committed
to the AP1000 power plant technology", plans to continue construction of
AP1000 plants in China and expects to bid for new plants in India and
elsewhere. She declined to comment on a detailed list of questions from
Reuters.
PROBLEMS FROM THE START
By early 2017, the Georgia and South Carolina plants were supposed to be
producing enough energy to power more than a half a million homes and
businesses. Instead, they stand half-finished. (For a graphic see
http://tmsnrt.rs/2oQEKgE)
Southern Co, which owns nearly half the Georgia project, and SCANA Corp,
which owns a majority of the South Carolina project, have said they are
evaluating the plants and could abandon the reactors altogether.
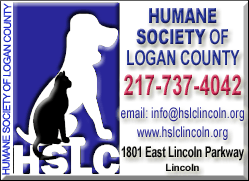
"We will continue to take every action available to us to hold
Westinghouse and Toshiba accountable for their financial
responsibilities under the engineering, procurement and construction
agreement and the parent guarantee," Southern said in a statement. A
spokesman declined to elaborate.
The projects suffered setbacks from the start. In one instance, to
prepare the Georgia plant for construction, Westinghouse and its
construction partner in 2009 began digging out the foundation, removing
3.6 million cubic yards of dirt.
But half of the backfill – the material used to fill the excavated area
- failed to meet regulatory approval, delaying the project by at least
six months, according to William Jacobs, the nuclear specialist who
monitored construction of the plant for Georgia's utility regulator.
He declined to be interviewed.
But the source of the biggest delays can be traced to the AP1000's
innovative design and the challenges created by the untested approach to
manufacturing and building reactors, according to more than a dozen
interviews with former and current Westinghouse employees, nuclear
experts and regulators.
Unlike previous nuclear reactors, the AP1000 would be built from
prefabricated parts; specialized workers at a factory would churn out
sections of the reactor that would be shipped to the construction site
for assembly. Westinghouse said in marketing materials this method would
standardize nuclear plant construction.
Westinghouse turned to Shaw Group Inc, which held a 20 percent stake in
Westinghouse, to build sections for the reactors at its factory in Lake
Charles, Louisiana. There, components for two reactors each in Georgia
and South Carolina would be manufactured.

[to top of second column] |
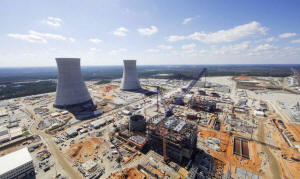
The Vogtle Unit 3 and 4 site, being constructed by primary contactor
Westinghouse, a business unit of Toshiba, near Waynesboro, Georgia,
U.S. is seen in an aerial photo taken February 2017. Georgia
Power/Handout via REUTERS

LAKE CHARLES
Seven months after work began in the May 2010, Shaw had already
conducted an internal review at the behest of the Nuclear Regulatory
Commission (NRC) to document problems it was having producing
components.
In a letter to the NRC, Shaw's then-executive vice president, Joseph
Ernst, wrote: "The level and effectiveness of management oversight
of daily activities was determined to be inadequate based on the
quality of work."
He laid out a laundry list of deficiencies ranging from Shaw's
inability to weed out incorrectly made parts to the way it stored
construction materials.
Ernst did not respond to a phone call seeking comment.
Over the next four years, regulatory and internal inspections at
Lake Charles would reveal a slew of problems associated with the
effort to construct modular parts to fit the new Westinghouse
design, NRC records show.
When a sub-module was dropped and damaged, Shaw managers ordered
employees to cover up the incident; components were labeled
improperly; required tests were neglected; and some parts'
dimensions were wrong. The NRC detailed each one in public violation
notices.
Then there was the missing and illegible paperwork.
The section that was delayed more than eight months by missing
signatures would become one of 72 modules fused together to hold
nuclear fuel. The 2.2 million pound unit was installed more than two
years behind schedule.
It was not until June 2015 that the Lake Charles facility was
building acceptable modules, according to a report by Jacobs. By
then, Shaw had been bought by Chicago Bridge & Iron.
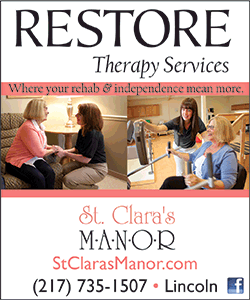
Gentry Brann, a CB&I spokeswoman, said the company put the Lake
Charles plant under new management and installed new procedures
after the 2013 acquisition. She said Westinghouse was to blame for
subsequent delays, citing "several thousand" technical and design
changes made after work had already started on various components.
Westinghouse declined to comment.
THE NRC
To some extent, Westinghouse also was hamstrung by the NRC, which
imposed stringent requirements for the new reactors. To comply,
Westinghouse made some design changes that were tiny tweaks; others
were larger.
For instance, before the NRC would issue the utilities an operating
license for the Georgia plant, it demanded changes to the design of
the shield building, which protects against radiation leaks. The
regulator said the shield needed to be strengthened to withstand a
crash by a commercial jet, a safety measure arising from the Sept.
11, 2001 attacks.
The NRC issued the new standard in 2009, seven years after
Westinghouse had applied for approval of its design. The company, in
bankruptcy court filings, said the NRC's demand created
unanticipated engineering challenges.
A spokesman for the NRC, Scott Burnell, said the changes should not
have come as a surprise, since the agency had been talking about the
stringent requirements for several years.
Westinghouse changed its design to protect against a jet crash, but
at that point the NRC questioned whether the new design could
withstand tornadoes and earthquakes.
Westinghouse finally met the requirements in 2011, according to a
report by Jacobs.
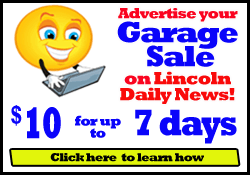
By 2016 Westinghouse began to grasp the scope of its dilemma,
according to a document filed in its bankruptcy: Finishing the two
projects would require Westinghouse to spend billions of dollars on
labor, abandoning them would mean billions in penalties.
Westinghouse determined it could not afford either option.
Graphic: Cost overruns at Westinghouse's nuclear plants -
http://tmsnrt.rs/2qnmtML
(Reporting by Tom Hals in Wilmington, Delaware; additional reporting
by Makiko Yamazaki in Tokyo; editing by Paul Thomasch)
[© 2017 Thomson Reuters. All rights
reserved.]
Copyright 2017 Reuters. All rights reserved. This material may not be published,
broadcast, rewritten or redistributed. |