Metal recyclers prepare for electric car revolution
Send a link to a friend
[November 17, 2017] By
Jan Harvey
LONDON (Reuters) - Recycling companies are
honing processes to extract metals from old batteries more cheaply and
efficiently so they can capitalize on an expected shortfall in materials
such as cobalt and lithium when sales of electric cars take off.
The main obstacle recyclers face now is a shortage of spent batteries to
recycle to make their technology cost-effective, but those at the
forefront of the industry are confident the supply, and profits, will
come.
"The value of lithium carbonate and natural or synthetic graphite has
doubled or tripled in the last three or four years, becoming the most
valuable materials besides cobalt in the automotive battery," Albrecht
Melber, co-managing director of German recycling firm Accurec, said.
"There are big values that can be recycled in the future."
Electric vehicle sales are expected to pass 14 million a year by 2025
from less than a million now, fuelling a surge in the consumption of
battery materials.(Graphic - Electric vehicles on the rise: http://tmsnrt.rs/2eNwQoZ)
Data specialist Benchmark Mineral Intelligence predicts the industry
will need an extra 30,000 tonnes of cobalt and 81,000 tonnes of lithium
a year to meet demand by 2021.
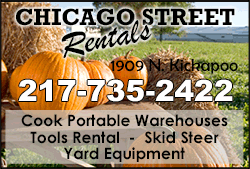
Commodity research group CRU expects 11,600 tonnes of cobalt to come
from recycling in 2021, up from 7,110 a year now, and 24,900 tonnes by
2026, accounting for 9.7 percent and 17.9 percent of the total market
supply respectively.
In China, where electric vehicle sales topped half a million last year,
recyclers are getting ready to deal with a mountain of battery waste and
others also see opportunities.
"A 1,000-pound lithium cobalt battery contains about $6,000 worth of
cathode material at the top end of the value chain and about $1,700 for
a nickel-cobalt-aluminum battery at the low end," said Larry Reaugh,
chief executive of Canadian metals recycler American Manganese <AMY.V>.
"If this equated to mining you would have a very high grade feedstock,"
he said. "We're mining batteries, you might say."
COBALT PRESSURE
Most electric cars are powered by lithium NMC batteries which use a
cathode composed of nickel, manganese and cobalt and a graphite anode.
Mining enough cobalt to meet demand is a particular concern as most of
the world's supplies come from Democratic Republic of Congo, where
mining areas are prone to conflict. The price of cobalt <COB-CATH-LON>
has more than doubled so far this year.
(Graphic - Demand for battery materials: http://reut.rs/2zzGHaG)
Supplies of lithium, mainly mined in Chile, are under far less pressure
at the moment and new production is due to come on stream in Argentina
and Australia.
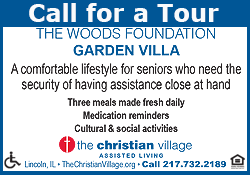
But concern the supply of lithium in battery-ready form will struggle to
keep pace with electric car sales has pushed prices up more than 30
percent to a record $12,000 a tonne this year.
Besides a shortage of old batteries to recycle, companies also face
challenges extracting lithium in a reusable form.
Most recyclers heat old batteries to high temperatures to retrieve
metals, a process known as pyrometallurgy. But this generally only
yields cobalt, and sometimes nickel, while lithium is more difficult and
expensive to extract.
The cost of recycling varies widely, but to be economical, CRU estimates
it would need to be transformed back into lithium carbonate at a maximum
cost of $7,000 a tonne.
For now, lithium usually ends up in waste slag, which can be used as a
building material, or is thrown away. But with the price of all these
metals rising, that picture may change.
MATERIAL MATRIX
Technological advances are key to retrieving more waste metal from
batteries and some companies say they have developed ways to get lithium
that will come into their own once there's a steady supply of spent
batteries to recycle.
Umicore <UMI.BR> uses a combination of pyrometallurgy and a chemical
process known as hydrometallurgy to retrieve lithium and rare earths
from slag, as well as extracting cobalt, nickel, and copper.
"A battery is a complex material matrix," Umicore says. "However, our
process allows (us) to separate and concentrate the lithium in one
process step, and yields alloys with cobalt, nickel and copper."
Umicore operates a pilot plant with a 7,000-tonne capacity that can
process some 35,000 electric vehicle batteries a year.
[to top of second column] |
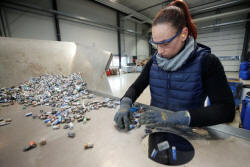
An employee sorts used primary non-rechargeable Lithium-ion
batteries before being recycled by the German recycling firm Accurec
in Krefeld, Germany, November 16, 2017. Picture taken November 16,
2017. REUTERS/Wolfgang Rattay
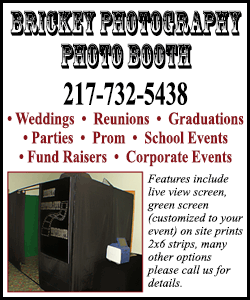
Analysts say the Belgian company, a well-established materials recycler, is by
far the most developed lithium ion battery processor in Europe.
"For investors to play the recycling theme, for now the best way is Umicore,"
said Tobias Bischoff, a portfolio manager at de Pury Pictet Turrettini & Cie who
advises NSF Wealth Management's Global New Mobility fund.
U.S. company Retriev Technologies has been recycling lithium ion batteries at
its plant in Trail, British Columbia, since 2002, recovering cobalt, nickel and
copper. It expanded a facility in Ohio to process lithium ion batteries two
years ago.
Between 2012 and the end of last year production at its Trail facility doubled,
with the plant processing about 1,200 tonnes of batteries. The company expects
growth at a similar rate over the next five years, vice president Todd Coy said.
Other companies are also pushing into lithium ion battery recycling. Accurec now
has a 1,000-tonne capacity demonstration plant for recycling car batteries at
its Krefeld facility in western Germany, though it says volumes remain small.
Australia's Neometals <NMT.AX> is building a pilot plant in Montreal, aiming to
develop processes tested in laboratories and small-scale plants for extracting
cobalt, lithium and nickel.
Also in Canada, American Manganese says it can retrieve 100 percent of the
lithium - as well as cobalt, nickel, manganese and aluminum - from batteries,
using technology originally developed to process low-grade manganese ores.
It has completed a proof of concept for its process and has a patent pending. A
pilot plant is the next step.
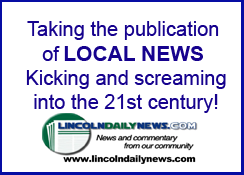
SECOND LIFE
But commercial development for recyclers is tough without the economies of scale
that will come with a greater supply of spent batteries. Retriev, for example,
says large volumes will be key to developing lithium recycling using
hydrometallurgy.
"At current commodity prices we need approximately 4,000 tonnes per year of
batteries to justify the estimated capital costs," Retriev's Coy said, more than
three times its current processing volumes.
"We are confident this volume will be coming in the future - beyond 2023 - but
the market is not there yet."
While electronic car sales are growing fast, lithium ion car batteries last
eight to 10 years on average, meaning it will be the best part of a decade
before significant numbers are spent.
American Manganese's Reaugh says it is planning to focus initially on recycling
material from faulty batteries to get around the wait for working batteries to
expire.
Even when they do, battery makers say many will have a second life as grid
storage, potentially for the best part of another decade. German carmaker BMW <BMWG.DE>,
for example, says its batteries are specifically designed for that purpose.
Grid storage systems use batteries no longer performing at levels to power cars
to store electricity which can be used to even out fluctuations in supply and
demand.
Still, not everyone is convinced grid storage will put the brakes on recycling.
"At the end of the day it's going to come down to whether the raw materials in
the battery are worth more than the battery as grid storage," CRU analyst George
Heppel said. "I think there will be a better incentive to recycle the materials,
and from there build a more efficient battery with new technology."
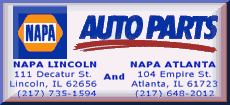
Umicore says it expects volumes of spent batteries to rise above 100,000 tonnes
a year in the next decade, with "massive volumes" coming onto the market around
2025. Once that happens, the opportunities for recyclers to capitalize will take
off.
"It definitely is a market that could become materially important," said
portfolio manager Bischoff. "We've looked at it, and we'll look at it again."
(Reporting by Jan Harvey; editing by David Clarke)
[© 2017 Thomson Reuters. All rights
reserved.] Copyright 2017 Reuters. All rights reserved. This material may not be published,
broadcast, rewritten or redistributed. |