Tesla's seat strategy goes against the
grain...for now
Send a link to a friend
[October 26, 2017]
By Alexandria Sage
SAN FRANCISCO (Reuters) - Elon Musk was fed
up.
The seats on Tesla Inc's <TSLA.O> new Model X SUV were a mess. An
outside contractor was having trouble executing the complicated design,
spurring frustration and finger-pointing between Tesla and its supplier.
How would Tesla ever pull off mass production of the upcoming Model 3,
the car intended to catapult the niche automaker into the big leagues,
if it could not deliver on something as fundamental as a seat?
Musk made a decision: Tesla would build the seats itself.
Tesla's demanding chief executive vowed years ago to shake up the
automotive industry with his line of electric vehicles and a futuristic
manufacturing facility in Fremont, Calif. But industry experts say
Musk's insistence on performing much of the work in-house is among the
reasons Tesla is nowhere close to its stated goal of building 500,000
vehicles annually by next year, most of them Model 3s.
The automaker this month revealed it built just 260 of the vehicles
between July and September, badly missing its target of 1,500 Model 3s
in the third quarter. In a statement, Tesla blamed manufacturing
"bottlenecks." It declined to elaborate, but assured investors "there
are no fundamental issues with the Model 3 production or supply chain."
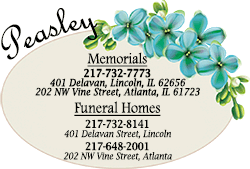
Tesla has demonstrated a commitment to vertical integration not seen in
the auto industry for decades.
The company has so far sunk $2 billion into a sprawling Nevada factory
to manufacture its vehicles' batteries. In-house programmers design the
bulk of the complex software that runs the Model 3, which Musk has
described as a "computer on wheels". Tesla controls its own retail
chain, selling its cars directly to customers and bypassing dealers.
But it is Tesla's 2015 decision to build its own seats that has some
industry veterans scratching their heads. Seat making is a low-margin,
labor-intensive enterprise that big automakers generally farm out to
specialists. Tesla is operating its own seat assembly line inside its
factory, and it is hiring engineers and technicians to figure out a way
to fully automate the process.
"Is that really the core competency of an auto company? It is not," said
analyst Maryann Keller, who has been tracking the car industry since the
early 1970s. "Why would you want to do that?"
Tesla declined requests from Reuters to discuss its seat assembly
efforts. The company is expected to reveal more about its production
issues on Nov. 1, when it announces third-quarter results. There is no
indication that the "bottlenecks" mentioned previously by the company
are associated with seat production.
Analyst Keller and others suspect Tesla eventually will be forced to
farm out seat assembly to suppliers as the company transitions from a
niche producer of pricey, hand-built luxury cars to a mass manufacturer.
Seat makers including Germany's ZF Friedrichshafen AG [ZFF.UL], France's
Faurecia SA <EPED.PA> and Detroit-based Lear Corp <LEA.N> already are
trying to win that business.
A lot is riding on Tesla's ability to scale up operations quickly.
Starting at $35,000, the Model 3 is Tesla's attempt to bring its
electric technology to a wider audience. More than a half-million
customers have already put down deposits.
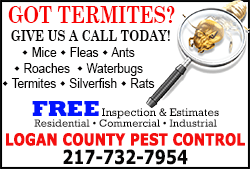
Tesla has never turned an annual profit and it is burning through cash.
Yet investors are betting big on its future. It is now the second most
valuable U.S. automaker, behind only General Motors Co <GM.N>. Tesla
shares on Wednesday closed at $325.84, down 3.4 percent.
FROM STOP-GAP TO STRATEGY
Musk has defended Tesla's hands-on approach as the way to ensure
reliability, as well as an opportunity to rethink industry norms.
It is also a reflection of the entrepreneur's obsession with detail.
"One of the hardest things to design is a good seat," Musk said at the
September 2015 launch of the Model X in Fremont.
[to top of second column] |
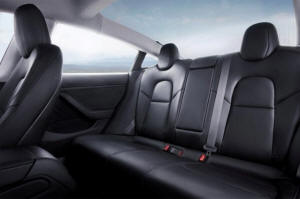
The interior of the Tesla Model 3 sedan is seen in this undated
handout image as the car company handed over its first 30 Model 3
vehicles to employee buyers at the company's Fremont facility in
California, U.S., July 28, 2017. Tesla/Handout via REUTERS
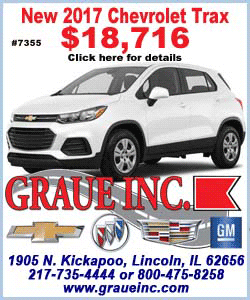
Problems first surfaced with the flagship Model S sedan in 2012.
Musk complained that the seats made by its contract manufacturer,
Australia-based Futuris Group, were not comfortable nor of the
quality expected for a car whose price tag started at around
$57,400, according to a former Tesla executive who described Musk's
thinking to Reuters.
Troubles accelerated with the Model X, leading Tesla to wrest
assembly from Futuris just after the vehicle's release in late 2015.
If seats could be entirely redesigned from the ground up, Musk
reasoned, maybe their assembly could be automated in preparation for
the high volumes anticipated for the Model 3.
"He saw the opportunity to do it differently and better," the former
Tesla executive said. "The short term was a stop gap, but the
long-term idea was to rethink the design of how a seat works to
include how a seat is built."
Futuris did not respond to requests for comment. It continues to
supply seat parts to Tesla. Detroit-based seating supplier Adient
PLC <ADNT.N> acquired Futuris for $360 million last month.
Meanwhile, Tesla's seat woes continue. In all, the automaker has
issued four seating-related recalls since 2013. The latest came this
month with the recall of 11,000 Model Xs manufactured between Oct.
28, 2016 and Aug. 16, 2017.
SUPPLIERS CIRCLING
Making car seats is a complex business. Choosing materials, dying
and cutting, shaping foam and metal frames, and adding heaters,
recliners and other gadgets can involve nearly a dozen suppliers for
top models. Final assembly requires lots of labor.
That's why most automakers opted decades ago to outsource seats for
their lower-cost models to specialty seatmakers whose market is
expected to reach $79 billion by 2022, according to market
researcher Lucintel.
Although Musk's philosophy has always been "build it right and then
figure out how to get the cost down" later, according to the
ex-Tesla executive, observers say Tesla can ill afford more
production headaches.
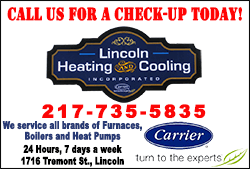
Philippe Houchois, an auto analyst with the investment bank
Jefferies, wrote in a September note to clients that "scalability"
was now the main challenge at Tesla, whose manufacturing prowess is
still unproven when it comes to building large numbers of vehicles.
"We don't think Tesla's vertically integrated business model can be
scaled up as profitably and quickly as consensus thinks," Houchois
wrote.
Despite Tesla's previous battles with Futuris, seat suppliers smell
opportunity. ZF Friedrichshafen and Faurecia have opened Silicon
Valley labs, in part to woo Tesla.
Lear, which cuts and sews material for Tesla, is likewise pressing
to get the automaker's seat manufacturing business, according to
Matthew Simoncini, the company's chief executive.
"In general Tesla has a philosophy: 'We'll do it ourselves. We'll
change the mold,'" Simoncini said. "(Outsourcing)is a much more
efficient use of capital. That would allow them to focus on what
they do best."
(Reporting By Alexandria Sage; Editing by Peter Henderson and Marla
Dickerson)
[© 2017 Thomson Reuters. All rights
reserved.]
Copyright 2017 Reuters. All rights reserved. This material may not be published,
broadcast, rewritten or redistributed.
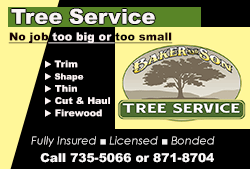 |