Boeing moves to keep 777X on track after engine snag
Send a link to a friend
[March 17, 2018]
By Tim Hepher
SEATTLE (Reuters) - Boeing Co <BA.N> has
scrambled to reorganize testing of its new 777X to avoid being delayed
by engine snags, while robots and mechanics are starting work on the
fuselage, the executive who heads efforts to build the world's largest
twin-engined jet said in an interview.
Engine supplier General Electric <GE.N> began flight trials of its new
GE9X jet engine on Tuesday after a three-month delay caused mainly by a
problem in its compressor. But to put the engine development back on
track it must build a new component.
During that time, Boeing will place two temporary engines on the first
flight-test aircraft that is gradually beginning to take shape, starting
with its lightweight carbon wings and now the fuselage, which Boeing
says is on schedule.
The engines, identical in every other respect to the ones that will go
into service, will be swapped for fresh ones with the new part before
the first 777X carries out its maiden flight next year. The temporary
engines will not be fired up, but having them in place will allow other
tests to go ahead.
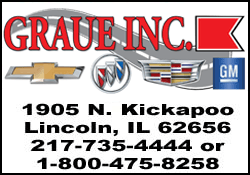
"Honestly, when this happened I thought 'this is going to be bad' and we
just kept grinding and grinding at it, and we came up with some pretty
creative things to test where we could, build where we could," 777X Vice
President and General Manager Eric Lindblad told Reuters.
"To put engines on and then take them off - that is all to protect the
schedule," Lindblad said.
The hurried rejig reflects the fact that after years of planning,
production has begun in earnest - something evident from activity inside
Boeing's new high-tech wing center.
"We are at the point where it is time to start scaling up the speed that
we build things here," Lindblad said inside the 1.3 million-square-foot
(120,800-square-meter) fabrication plant where machines weave and bake
major parts of the carbon wings.
The engine swap is also an example of how Boeing is trying to avoid
eating into the 'buffer' traditionally built into development schedules.
That's because it faces a challenging two years before the latest
version of its 777 enters service.
"We are now in the thick of it ... There is no more waiting until later
to solve problems," Lindblad said. "There are still two years left. You
cannot give away your buffer."
The 777X aims to maintain Boeing's grip on the 'mini-jumbo' market by
leapfrogging Airbus SE's <AIR.PA> 365-seat A350-1000. Boeing has sold
over 300 jets, though activity has slowed.
'MORE OPTIMISTIC'
So far, Boeing says it is on track to meet a 2020 target for delivering
the first 406-seat 777-9 model to Emirates Airline.

[to top of second column] |
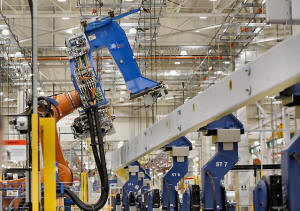
A wing spar assembly robot is pictured during a launch event for the
Boeing 777X at the Boeing production facility in Everett,
Washington, U.S. October 23, 2017. REUTERS/Jason Redmond/File Photo
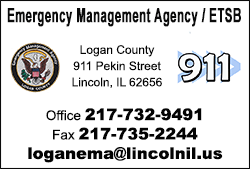
But although the engine snag marks the first significant public slippage, Boeing
has already faced a number of teething problems in building carbon wings and
other components.
"Everything is hard at this point where you start building an airplane. When you
ask me how wing assembly has been going, it's been hard," Lindblad said.
One of the problems involves fitting the carbon panels to the skeleton of spars
and ribs, with the light but strong carbon-fiber material less forgiving than
traditional aluminum.
"Assuming we continue to march our way through the plan that we have laid out, I
feel pretty optimistic about (the engine) and I think that wing assembly is a
matter of incorporating the learnings," Lindblad said.
Six months ago, Lindblad says something else was making him feel "queasy".
Integration of aircraft systems in a special demonstration lab was not happening
as quickly as planned.
"I am more optimistic today," he said. He added that he would be "cautiously
guarded" until the first flight, due in the first quarter of 2019.
Another headache has been producing enough wing stringers: reinforcing strips
that go outwards from the fuselage.
"I feel confident we have got a plan for that so we are tracking basically back
to schedule."
Now Boeing must marry together the various wing parts and produce the long
metallic fuselage.
Fuselage panels arriving from Japan have been loaded into a "Fuselage Automated
Upright Build" (FAUB) machine used to fasten them. Boeing had delays when the
machine was tried out on existing versions of the 777, but Boeing says the
system is now running at full speed of five planes a month.
Drawing on experience of the smaller 737 MAX, which has absorbed production
increases on a larger scale, Lindblad said the 777X production system had been
set up to handle a targeted speed but would not disclose capacity.
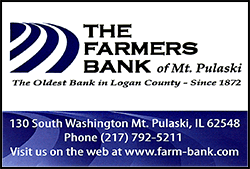
"We are planning for world demand," he said.
The first task is to get flight trials under way so that ambitious fuel-saving
goals can be tested.
"Will we get four airplanes in the flight test on schedule? We'll see. I think
we have a pretty good shot at it."
(Reporting by Tim Hepher in Seattle; editing by Grant McCool)
[© 2018 Thomson Reuters. All rights
reserved.] Copyright 2018 Reuters. All rights reserved. This material may not be published,
broadcast, rewritten or redistributed.
Thompson Reuters is solely responsible for this content. |