Sweden's SKF to shift automation into higher gear as markets flag
Send a link to a friend
[September 19, 2019] By
Johannes Hellstrom
GOTHENBURG (Reuters) - Swedish engineering
company SKF aims to use a demand slowdown to its advantage, its chief
executive said, stepping up an automation program that has already sent
capital expenditure soaring.
SKF, which supplies bearings to automotive and industrial markets, has
automated manufacturing at a string of plants, but the bulk of its 94
factories still need to be tackled.
"There has been a long period where we have had to fight to keep up with
the high demand in some factories, and you can't rebuild plants in a
situation like that," Alrik Danielson told Reuters.
"So it's clear that some of these activities will accelerate now."
The world's biggest ball-bearings maker, which supplies the likes of
carmakers Tesla and Volkswagen <VOWG_p.DE> as well as wind turbine
makers, in July posted its first quarterly decline in organic sales
since 2016.
That pause to years of sharp growth was accompanied by a forecast for
slightly lower demand year on year in the third quarter, with stable
demand for its industrial business and lower volumes for automotive.
Danielson, at the helm since 2015, has pushed a revamp of the factory
network, cutting the number of plants, moving manufacturing to better
match customer demand and investing in automation, bringing job cuts in
their hundreds on affected assembly lines.
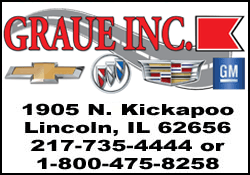
The Gothenburg-based company, the products of which are found in most
machinery with rotating parts, expects 2.8 billion crowns ($288 million)
in capital spending this year, up 50% from 2016.
Danielson said that higher future investment is being considered and
lauded the payback on previous projects.
"I have to say that the returns on these investments are very good, so I
am not worried about that."
SKF has previously automated parts of its production in Gothenburg as
well as at its plant in Schweinfurt, Germany, and a U.S. factory at
Flowery Branch, Georgia, among others.
It has already flagged plans for a new factory in Xinchang, China, while
slimming down in Bari, Italy, where it would build an automated
production channel.
The automation of one production channel in Gothenburg in 2016 left 20
workers to run a process that had previously required 100 workers.
[to top of second column] |
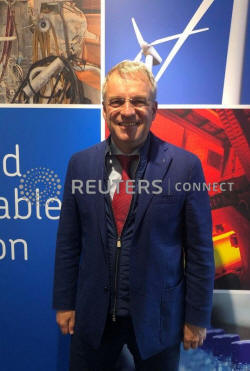
SKF CEO Alrik Danielson poses for a picture at SKF headquarters in
Gothenburg, Sweden September 11, 2019. REUTERS/Johannes Hellstrom
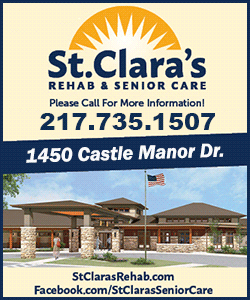
While the simple hammer would have been much in evidence previously, the switch
to automation has brought lower lead times, higher quality and greater
flexibility. This, in turn, means SKF can remain competitive on cost for
smaller, custom-made orders. WAIT-AND-SEE MARKETS
Many of SKF's markets are in a wait-and-see mode pending more clarity on the
U.S.-China trade war and the outcome of Britain's planned exit from the European
Union, but a pent-up need for technology investments could act as a cushion,
Danielson said.
"Sure it's weaker, and we have said that, but it is not a disaster by any means.
My feeling is that it is largely wait-and-see (markets) currently," he said.
Danielson added that the changing technology landscape, with automation,
electrification, sensor and analytic tools also encourages investment to
capitalize on new business models.
"What's very interesting is that the rapid technology change provides an
underlying incentive to invest," he said.
"Even if you sit in your boardrooms and are not investing in capacity, you know
that you need to modernize your plants to remain competitive."
Many analysts have questioned SKF's ability to defend its margins when demand is
weakening for a business that has historically been sensitive to cyclical
downturns.
Danielson counters this by pointing to far higher margins last year than in the
company's peak years before the financial crisis.
"I am convinced that we are much better prepared to handle demand swings today
than we used to be," he says.
(Reporting by Johannes Hellstrom; Editing by Keith Weir and David Goodman)
[© 2019 Thomson Reuters. All rights
reserved.] Copyright 2019 Reuters. All rights reserved. This material may not be published,
broadcast, rewritten or redistributed.
Thompson Reuters is solely responsible for this content.
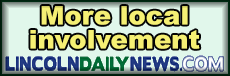 |