The United States had equipment to provide ventilation - which is
needed to help patients breathe when they can no longer do so on
their own - to about 160,000 people, according to research compiled
by the Johns Hopkins Center for Health and Security.
But as the outbreak ramps up, tens of thousands more units will be
needed, which has prompted automakers and others to look at how to
make them. President Donald Trump on Friday signed an order
requiring carmaker General Motors Co <GM.N> to produce ventilators
to fight the coronavirus pandemic under the Defense Production Act,
accusing the automaker of "wasting time."

The shortage has prompted medical device firms to scale up fast.
Darren Saravis, CEO of Long Beach, California-based medical device
engineering firm Nectar Inc, launched a new company BreathDirect to
make a slimmed-down version of a ventilator. The new device will
cost about $10,000 and has simpler settings than other models.
Saravis said it will be faster to manufacture but can still handle
the needs of about 90% of critical care patients.
"For me, this is really about me not having any other choice. I
would never have been able to live with myself if I didn't step up
and do this because I have the ability, I have the team, we have the
resources here, and I don't want to wake up and know that I was
responsible for people not living," Saravis said.
[to top of second column] |
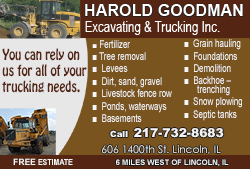
BreathDirect aims to complete its first unit by April 5, with its first
production-ready ventilator made by April 19, Saravis said, though exact timing
depends on approval by the U.S. Food and Drug Administration. Eventually, it
hopes to produce 3,500 ventilators per week by May and 40,000 ventilators per
month in June, Saravis said.
To hit the deadline, Saravis tapped contract manufacturer Evolve Manufacturing
Technologies Inc, a Fremont, California-based company already registered with
the FDA and is also making coronavirus test kits. Noreen King, Evolve's chief
executive, said the company, which also works on ultrasound machines and spinal
surgery products, has pushed aside about 10% of current projects to focus on
equipment for the pandemic.
"When I was listening to the news, and everyone was really dying for these
ventilators, I realized this is such a tragic thing because I understand how
difficult it is to make," King said.
(This story has been refiled to fix garble in second paragraph)
(Reporting by Nathan Frandino in Fremont, California; writing by Stephen Nellis
in San Francisco; Editing by David Gregorio)
[© 2020 Thomson Reuters. All rights
reserved.] Copyright 2020 Reuters. All rights reserved. This material may not be published,
broadcast, rewritten or redistributed.
Thompson Reuters is solely responsible for this content.
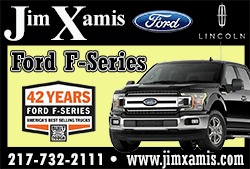 |