The robot apocalypse is hard to find in America's small and mid-sized
factories
Send a link to a friend
[August 02, 2021] By
Timothy Aeppel
CLEVELAND (Reuters) - When researchers from
the Massachusetts Institute of Technology visited Rich Gent's machine
shop here to see how automation was spreading to America's small and
medium-sized factories, they expected to find robots.
They did not.
"In big factories - when you're making the same thing over and over, day
after day, robots make total sense," said Gent, who with his brother
runs Gent Machine Co, a 55-employee company founded by his
great-grandfather, "but not for us."
Even as some analysts warn that robots are about to displace millions of
blue-collar jobs in the U.S. industrial heartland, the reality at
smaller operations like Gent is far different.
Among the 34 companies with 500 employees or fewer in Ohio,
Massachusetts and Arizona that the MIT researchers visited in their
project, only one had bought robots in large numbers in the last five
years - and that was an Ohio company that had been acquired by a
Japanese multinational which pumped in money for the new automation.
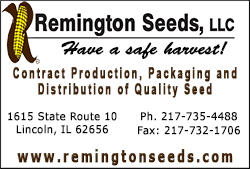
In all the other Ohio plants they studied, they found only a single
robot purchased in the last five years. In Massachusetts they found a
company that had bought two, while in Arizona they found three companies
that had added a handful.
Anna Waldman-Brown, a PhD student who worked on the report with MIT
Professor Suzanne Berger, said she was "surprised" by the lack of the
machines.
"We had a roboticist on our research team, because we expected to find
robots," she said. Instead, at one company, she said managers showed
them a computer they had recently installed in a corner of the factory -
which allowed workers to note their daily production figures on a
spreadsheet, rather than jot down that information in paper notebooks.
"The bulk of the machines we saw were from before the 1990s," she said,
adding that many had installed new computer controllers to upgrade the
older machines - a common practice in these tight-fisted operations.
Most had also bought other types of advanced machinery - such as
computer-guided cutting machines and inspection systems. But not robots.
Robots are just one type of factory automation, which encompasses a wide
range of machines used to move and manufacture goods - including
conveyor belts and labeling machines.
Nick Pinkston, CEO of Volition, a San Francisco company that makes
software used by robotics engineers to automate factories, said smaller
firms lack the cash to take risks on new robots. "They think of capital
payback periods of as little as three months, or six - and it all
depends on the contract" with the consumer who is ordering parts to be
made by the machine.
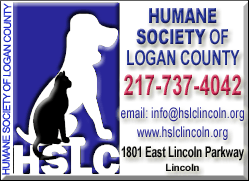
This is bad news for the U.S. economy. Automation is a key to boosting
productivity, which keeps U.S. operations competitive. Since 2005, U.S.
labor productivity has grown at an average annual rate of only 1.3% -
below the post-World War 2 trend of well over 2% - and the average has
dipped even more since 2010.
Researchers have found that larger firms are more productive on average
and pay higher wages than their smaller counterparts, a divergence
attributed at least in part to the ability of industry giants to invest
heavily in cutting-edge technologies.
Yet small and medium-sized manufacturers remain a backbone of U.S.
industry, often churning out parts needed to keep assembly lines rolling
at big manufacturers. If they fall behind on technology, it could weigh
on the entire sector. These small and medium-sized manufacturers are
also a key source of relatively good jobs - accounting for 43% of all
manufacturing workers.
LIMITATIONS OF ROBOTS
One barrier for smaller companies is finding the skilled workers needed
to run robots. "There's a lot of amazing software that's making robots
easier to program and repurpose - but not nearly enough people to do
that work," said Ryan Kelly, who heads a group that promotes new
technology to manufacturers inside the Association for Manufacturing
Technology.
[to top of second column] |
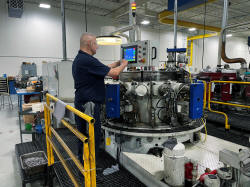
A worker operates one of the metal cutting machines at Gent Machine
Co.'s factory in Cleveland, Ohio, U.S., May 26, 2021.
REUTERS/Timothy Aeppel
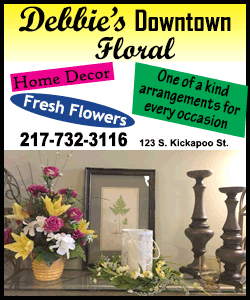
To be sure, robots are spreading to more corners of the industrial economy, just
not as quickly as the MIT researchers and many others expected. Last year, for
the first time, most of the robots ordered by companies in North America were
not destined for automotive factories - a shift partly attributed to the
development of cheaper and more flexible machines. Those are the type of
machines especially needed in smaller operations.
And it seems certain robots will take over more jobs as they become more capable
and affordable. One example: their rapid spread in e-commerce warehouses in
recent years.
Carmakers and other big companies still buy most robots, said Jeff Burnstein,
president of the Association for Advancing Automation, a trade group in Ann
Arbor, Michigan. "But there's a lot more in small and medium-size companies than
ever before."
Michael Tamasi, owner of AccuRounds in Avon, Massachusetts, is a small
manufacturer who recently bought a robot attached to a computer-controlled
cutting machine.
"We're getting another machine delivered in September - and hope to attach a
robot arm to that one to load and unload it," he said. But there are some tasks
where the technology remains too rigid or simply not capable of getting the job
done.
For instance, Tamasi recently looked at buying a robot to polish metal parts.
But the complexity of the shape made it impossible. "And it was kind of slow,"
he said. "When you think of robots, you think better, faster, cheaper - but this
was kind of the opposite." And he still needed a worker to load and unload the
machine.
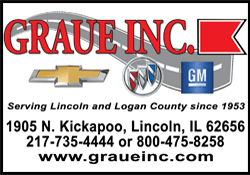
For a company like Cleveland's Gent, which makes parts for things like
refrigerators, auto airbags and hydraulic pumps, the main barrier to getting
robots is the cost and uncertainty over whether the investment will pay off,
which in turn hinges on the plans and attitudes of customers.
And big customers can be fickle. Eight years ago, Gent landed a contract to
supply fasteners used to put together battery packs for Tesla Inc - and the
electric-car maker soon became its largest customer. But Gent never got
assurances from Tesla that the business would continue for long enough to
justify buying the robots it could have used to make the fasteners.
"If we'd known Tesla would go on that long, we definitely would have automated
our assembly process," said Gent, who said they looked at automating the line
twice over the years.
But he does not regret his caution. Earlier this year, Tesla notified Gent that
it was pulling the business. "We're not bitter," said Gent. "It's just how it
works."
Gent does spend heavily on new equipment, relative to its small size - about
$500,000 a year from 2011 to 2019. One purchase was a $1.6 million
computer-controlled cutting machine that cut the cycle time to make the Tesla
parts down from 38 seconds to 7 seconds - a major gain in productivity that
flowed straight to Gent's bottom line.
"We found another part to make on the machine," said Gent.
(Reporting by Timothy Aeppel in Cleveland; Editing by Matthew Lewis)
[© 2021 Thomson Reuters. All rights
reserved.] Copyright 2021 Reuters. All rights reserved. This material may not be published,
broadcast, rewritten or redistributed.
Thompson Reuters is solely responsible for this content.
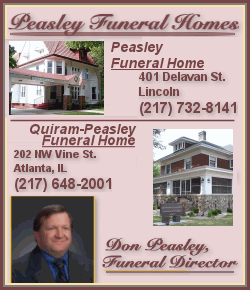 |