One U.S. company's risky effort to build a new mask factory during COVID
Send a link to a friend
[February 05, 2021]
By Timothy Aeppel
LA VERNE, Calif. (Reuters) - Dan Izhaky is
betting $4 million that the pandemic will change what Americans are
willing to pay for high quality face masks from his new factory here in
this suburb of Los Angeles.
It’s a risky wager.
Before COVID-19 hit, the United States imported much of the personal
protection equipment needed by health care providers, mainly from Asia.
Some U.S. companies pivoted in the crisis, such as liquor companies
churning out hand sanitizer and plastics firms making face shields.
But one item that remains in tight supply is N95 face masks, which
provide a high level of filtration against airborne contaminants and are
closely regulated by the U.S. government.
Izhaky is president of United Safety Technology Inc, a startup that is
poised to open a new N95 mask factory possibly within weeks. While the
plant is still being fitted with machinery, his goal is to make 1
million masks a day when it’s up and running. Izhaky said if they get
approval from regulators soon, the plant could be shipping that amount
by the end of the second quarter.

“The big question we face is what happens post-pandemic,” said Izhaky,
“when you have a hospital administrator or whoever it is that’s in
charge of purchasing” and looking at U.S.-made masks that cost more. The
pricing of many types of protective equipment remain elevated by
shortages, but once the market normalizes Izhaky estimates his masks
will cost about 30% more than Chinese masks, or about $1.15 each.
Other domestic producers are likely to face the same challenge,
including industry giants Izhaky will compete with. 3M Co has quadrupled
its domestic production of N95 masks since the start of the pandemic,
expanding a factory in South Dakota and hiring 300 workers and now makes
nearly 100 million masks in the U.S. a month. Honeywell International
Inc has opened “multiple new locations in the Phoenix area” to make N95
masks, said spokesman Eric Krantz, and converted a significant portion
of a factory in Rhode Island that also makes safety glasses.
Krantz said Honeywell doesn't view the expansion as a risk.
“We’re confident there will be continued demand for high-quality
respiratory protection products," he said in an email. "We’ve made
smart, strategic investments in expanding our N95 production."
But many smaller producers aren't so sure.
“China subsidizes their face masks,” so every producer faces a challenge
in competing with China after the pandemic, said Vitali Servutas, CEO of
AmeriShield, which built a factory that makes single-use surgical masks,
not N95 masks, in Virginia last year in response to the crisis.
Izhaky hopes, but is not certain, that the pandemic will make Americans
more willing to pay a premium, or that U.S. government policy will
mandate more domestic sourcing which would benefit his venture. Actions
by the incoming administration of President Joe Biden, including an
executive order aimed at increasing the production of a wide range of
goods in domestic factories through Buy American programs, have made him
more optimistic.
[to top of second column]
|

Masks are produced at United Safety Tech, a startup that is poised
to open a new N95 mask factory in La Verne, California, U.S.,
January 27, 2021. REUTERS/Timothy Aeppel
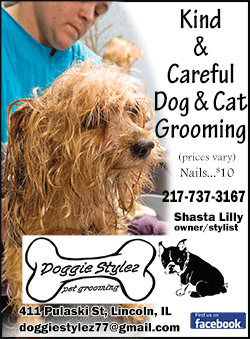
David Sanford, the brigadier general who directs the supply chain
advisory group at the Department of Health and Human Services
working on COVID-19 response, has been helping Izhaky and other
manufacturers work through the process of getting certified and
connected to domestic distributors of medical goods. He said
Izhaky’s new factory is exactly the kind of project the U.S. needs
to encourage.
“But there’s always a risk,” said Sanford. He adds there are ways
the government can support businesses like this, short of giving
direct government contracts to purchase goods at higher prices. A
requirement to buy U.S.-made protective equipment could be built
into Medicare and Medicaid reimbursements, for instance.
Making masks isn’t that hard. The process is highly automated and
doesn’t require a costly cleanroom. But getting a dependable supply
of the materials, particularly the specialized layers of filtration
material that makes them effective, is a challenge.
“You can buy a face mask machine for a few hundred thousand dollars
and start it up in 90 days. That’s happening all over the world,”
said Sara Greenstein, CEO of Lydall Inc, a U.S. producer of the
material that has agreed to supply Izhaky’s operation.
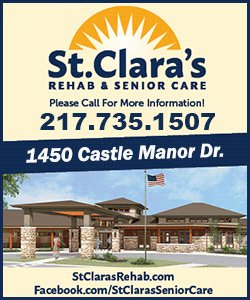
Lydall, aided by federal funds provided early in the crisis, has
nearly tripled capacity at its one U.S. plant capable of making the
material. With competing Chinese material expected to continue to
sell at much lower prices after the pandemic, Lydall CEO Greenstein
has "high confidence" there will be government-led programs in the
United States and Europe "to buy product made here to help keep that
supply chain stable and competitive.”
At the United Safety Technology plant in La Verne, engineers are
busy fine tuning the first of the machines that will eventually turn
out cup-shaped masks.
Edward Zheng, Izhaky’s partner in the venture, said their goal is to
source all the materials domestically, with a key exception: the
machines that make the masks in the factory are imported from China.
(Reporting by Timothy Aeppel; editing by Dan Burns and Edward Tobin)
[© 2021 Thomson Reuters. All rights
reserved.] Copyright 2021 Reuters. All rights reserved. This material may not be published,
broadcast, rewritten or redistributed.
Thompson Reuters is solely responsible for this content. |