Vice President Kamala Harris caught a glimpse of the unfolding
problem during her recent swing through Asia. In Singapore, a global hub for
maritime trade, she learned that congestion at its piers was causing shipping
companies to bypass the port.
What the vice president saw in Singapore and other ports in Vietnam and China
critical to global supply chains is a product of COVID-19. The Chinese port of
Ningbo, the world's third-largest, was closed for two weeks in August by
authorities over a single COVID case.
In Singapore, Harris commented that the shipping backlogs might
make it hard for Christmas shoppers to have gifts on time. But the challenges
are weightier than that. Our national security apparatus maintains lean
inventories and relies on just-in-time manufacturing and delivery – often from
overseas suppliers – to replenish their stocks. Shipping delays can create
serious vulnerabilities.
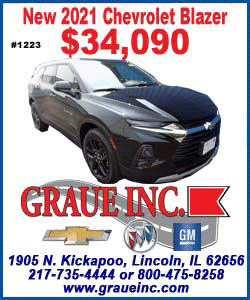
The slowdown is already hitting home. In Los Angles, a key port for U.S. trade
with Asia, historic shipping backlogs have resulted in a horizon full of ships
at anchor waiting to enter port. The backlog is even impacting Midwest rail
service and causing delays in air freight at major air hubs. For trade in
perishables like fruit, delays are a deal killer; as winter approaches,
consumers will find less fruit at the grocers.
The COVID-19 pandemic has hit global shipping and manufacturers with labor
shortages for 20 months now. This problem was compounded when a large container
ship grounded in the Suez Canal, blocking the waterway for six days. The
cascading effects of these misadventures have created delays that will take
months, if not longer, to resolve.
These delays are compounding the backlogs by driving a shortage of shipping
containers as ships wait at anchor to offload and reload. Container ships carry
13% of global trade by volume, accounting for 11% of global trade value.
Shippers want cargo in standard containers, driving producers to look for
replacements as too many are held up at sea, driving a surge in demand for
shipping containers. Yet container production is located overwhelmingly in
China, and supply is not likely to meet demand anytime soon.
Another problem is rising container shipping costs. On
Asia-West Coast U.S. routes, they have soared from $1,485 per 40-foot equivalent
unit in 2017 to rates ranging from $18,000 to $25,000 per FEU. With options
limited by the container shortage, exporters-importers are over a barrel. Some
shippers break contracted fees even after cargo is loaded, and this adds not
only cost but new uncertainty to global trade.
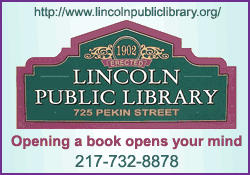
[to top of second column] |
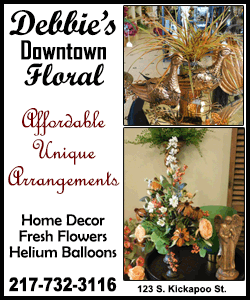
The global shipping backlog, combined with a COVID-related
dearth of truck drivers, is already disrupting U.S. assembly lines.
Inventory-to-sales rates are at the lowest-ever levels. Ordinarily,
supply and demand would result in more shipping companies and truck
drivers entering the market, but that hasn’t happened for several
reasons, including delayed re-entry into the workforce given
generous unemployment benefits.
The foremost challenge in this quiet crisis is
inflation – driven in part by higher shipping, labor and limited
availability of resources and parts. However, the more insidious
impact could be in the area of national security.
As The Heritage Foundation’s Maiya Clark points out, U.S. defense
supply chains rely on a global network of manufacturers – access to
which is being complicated by the shipping crisis. For years
manufacturers have relied on lean inventories or just-in-time
manufacturing, leaving little surge capacity for increased
production or to mitigate disruptions such as a Suez Canal
grounding.
Consider how a shortage of microchips slowed U.S. car manufacturing
early in the pandemic. Now consider the impact supply disruptions
could have on the nation’s next Columbia-class nuclear ballistic
missile submarine. Supply delays among any of the sub’s 5,000
suppliers could imperil delivery, which must occur before 2028 to
ensure the nation’s strategic deterrence.
No reports of production delays have been reported
as yet. But no one in or outside of the Pentagon fully understands
the extent to which Navy suppliers rely on overseas sources – a
truly troubling knowledge gap.
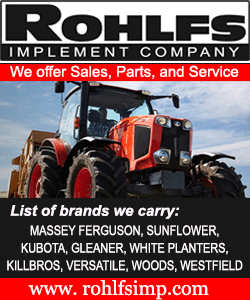
Events of the past six months offer some important lessons for the
military. First, it needs to have a more complete understanding of
its supply chains and actively diversify production as appropriate.
Second, today’s limited port infrastructure and transportation
workforce create bottlenecks that could impair wartime and crisis
logistics. Three, given recent supply disruptions, the military
needs to assure Congress that ‘lean inventories’ and ‘just in time’
manufacturing will not imperil success in a future war.
While no one looks forward to depleted store shelves during the
Christmas shopping season, the bigger concern for Americans should
be higher fuel bills, lack of fruit in the winter, and whether our
military can keep us safe while they wait for parts.
Brent D. Sadler is the senior fellow for naval
warfare and advanced technology at The Heritage Foundation’s Center
for National Defense.
|