U.S. factories pop up to make medical gloves, spurred by pandemic
Send a link to a friend
[June 21, 2022]
By Timothy Aeppel
FAYETTE, Alabama, (Reuters) - Rising from a
muddy field on the outskirts of the small town of Fayette, Alabama is a
bricks-and-mortar symbol of the global COVID pandemic: A new glove
factory.
When completed in 2024 the complex, owned by Japan’s SHOWA Glove Co will
be able to produce about 3 billion medical-grade nitrile gloves a year
from its dozen massive new, five-stories-tall, automated assembly lines.
That may seem like a lot but is only a small slice of the over 100
billion consumed in the United States annually.
"There’s a burgeoning glove manufacturing industry popping up in this
country, a lot of it funded by the government," said Dan Izhaky, chief
executive of New York-based United Safety Technology, which got $96
million in federal backing to begin to transform an empty Baltimore
steel plant.
Demand for gloves spiked early in the pandemic, spotlighting a glaring
weakness in the U.S. supply chain for all types of medical safety
equipment. Most of it comes from factories in Asia.
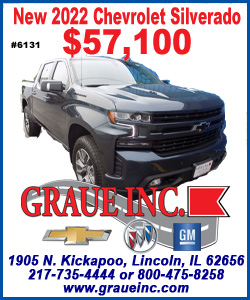
"The market went absolutely crazy during the pandemic," said Richard
Heppell, head of SHOWA's U.S. division, as buyers scrambled to find
supplies and prices exploded.
SHOWA was expanding a small, decades-old glove factory in Fayette -
originally built to make old-style latex gloves - when the pandemic
struck. Seeing an opening for a revival of larger-scale U.S. glove
manufacturing as the government reconsidered the wisdom of heavily
relying on foreign sources, the company decided to triple the size of
its expansion.
At least 12 other companies - a mix of domestic startups and Asian and
U.S. producers looking to gain or expand U.S. footholds - are building
new glove plants, including the one inside the former Baltimore steel
mill and another in a former Caterpillar factory outside Chicago. One
entrepreneur wants to build a plant on a Navajo reservation in New
Mexico.
The U.S. Department of Health and Human Services (HHS) has so far
committed $572 million to five glove projects, including $81.3 million
for SHOWA, "that will result in domestic capacities that can produce
more than 600 million nitrile gloves per month," according to a HHS
spokesperson.
PANDEMIC-RELATED BUSINESS RISKS
Izhaky knows the risks of jumping into a pandemic-related business.
He and a partner hastily built a face mask factory with private funds in
Los Angeles early in the COVID crisis but was forced to shutter it when
mask prices collapsed and customers evaporated. Most of the mask
factories that sprang up during the pandemic have closed.
Despite that experience, Izhaky and other producers are counting on
customers willing to pay some premium for U.S.-made gloves, as well as
federal mandates such as requiring them in government safety stockpiles.
A group of glove makers are discussing forming a trade group to push for
such mandates and lobbying is underway, company officials said.
[to top of second column]
|
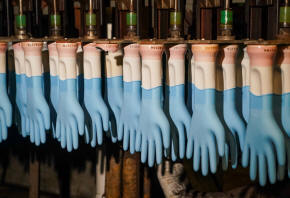
Original nitrile glove producing machinery is pictured at a factory
of SHOWA, a large Japanese glove producer, in Fayette, Alabama,
U.S., June 2, 2022. REUTERS/Marvin Gentry
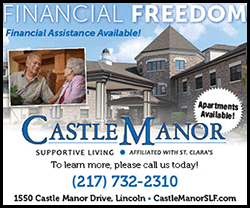
"The VA, DHS, TSA, they all use huge
amounts of gloves," said Izhaky, reeling off a list of federal
agencies. "We’re expecting that they’ll be mandated to purchase Made
in America."
But it remains a risky proposition. The Biden administration has not
guaranteed it will buy the output of these new operations, and the
cost of producing domestically, even using the latest equipment, is
expected to remain higher than imports.
Glove making is far more capital intensive than
masks, raising the stakes for those building large factories.
Modern glove factories are modeled on those developed in Asia, a
reverse of the decades-old pattern of companies in advanced
economies developing industries in low-cost regions. Izhaky’s
project has 45 U.S. employees and a team of 28 in Malaysia with
industry experience.
Alison Bagwell is an American engineer who spent most of her career
working for Kimberly-Clark, setting up glove factories in Thailand
and Malaysia. With private backing, she is building a $70 million
plant in Sandersville, Georgia, set to open next year.
"I feel pretty confident that I can do this," she
said, "having done it in a third world country."
In Fayette, the SHOWA factory is churning out gloves in the original
production area and a towering new addition that holds the first
four new production lines. Behind the building, a new structure for
four additional lines is nearly complete, while another four-line
building has yet to break ground.
Plant manager Scott Robertson leads the way past a team of women
catching clumps of blue gloves as they are automatically pulled off
ceramic hands used to mold them and piled into stacks.
"We have to use these auto stackers," he said, referring to the
machines that gather the gloves, "because gloves are coming off the
line so fast there’s no way a person could keep up."
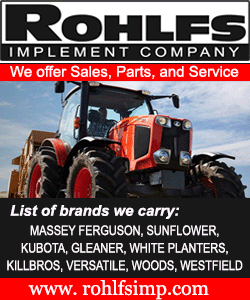
The company is planning to install new machinery in this spot that
will do the job of putting the gloves into boxes.
"We have to do everything we can to control cost," said Gilbert
LeVerne, the company’s marketing director, "because this country is
cost impulsive - the disaster goes away and the mindset shifts back
to the bottom line."
(Reporting by Timothy Aeppel; Editing by Bill Berkrot)
[© 2022 Thomson Reuters. All rights
reserved.]
This material may not be published,
broadcast, rewritten or redistributed.
Thompson Reuters is solely responsible for this content. |