Austin, we have a problem! Tesla descends into battery hell
Send a link to a friend
[December 21, 2023] By
Norihiko Shirouzu and Paul Lienert
AUSTIN, Texas (Reuters) - Elon Musk says prototypes are easy, production
is hell. And when it comes to the long-awaited Cybertruck, Tesla's hell
is its pioneering 4680 battery.
Tesla delivered the first of its futuristic stainless steel-plated
electric pickups last month and CEO Musk said in October that it would
probably hit an annual production rate of a quarter of a million
vehicles at some point during 2025.
But Tesla is still a long way off that kind of production pace, and one
of the main bottlenecks is the speed it can make the 4680 batteries used
in the Cybertruck with its new dry-coating technology, nine people
familiar with the matter said.
Tesla's Giga Texas factory is currently churning out 4680 battery cells
at rate only sufficient to power about 24,000 Cybertrucks a year, or
about a 10th of the required output, according to Reuters calculations
based on a combination of public data and unpublished figures provided
by sources.
Being able to ramp up battery output massively by dry-coating electrodes
- rather than using the slower, more costly wet-coating - was a key
factor behind Tesla's forecasts in 2020 that it would more than halve
battery costs, cut investment significantly, and create smaller, greener
factories.
The nine people, who spoke to Reuters on condition of anonymity because
of the sensitivity of the matter, said Tesla had yet to crack
dry-coating at the industrial scale needed to make 4680 batteries fast
enough to hit its production targets.
The people said dry-coating the anode in the 4680 cells was not
problematic but Tesla was struggling with the same technique for the
cathode - the most expensive component in a battery.
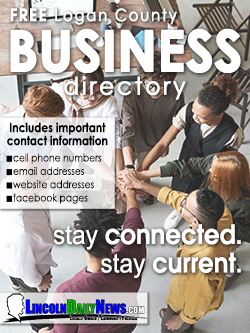
Dry-coating anodes and cathodes is proven in the laboratory, as well as
for smaller energy storage devices such as super capacitors, and even
some small batteries, according to Yuan Gao, a battery technology
consultant.
"But no one has done it so far for large EV batteries at a mass scale
and at a high enough speed. Tesla is the first one to try to
commercialize this," said Gao, who has worked in the industry for three
decades.
"The challenge is that not only does Tesla have to scale it up and speed
up the process, it also must develop its own equipment and tools. It's
daunting to say the least," he said.
Tesla did not respond to detailed questions from Reuters for this story.
CRACKING THE CODE
According to three of the sources, the 4680 batteries in Cybertrucks
include an estimated 1,360 individual cells.
That means Tesla would need to make 340 million cells a year, or almost
a million a day, to supply 250,000 of the electric pickups, which are
entering a hot market with rivals such as Ford's F-150 Lightning,
Rivian's R1T and an electric Hummer from General Motors.
At the moment, Tesla's Austin factory takes about 16 weeks to make 10
million 4680 cells, according to Reuters calculations based on figures
from Tesla, verified by the three sources.
That translates to 32.5 million cells a year, or enough for just under
24,000 pickups - and that's only for the Cybertruck.
Tesla also wants to use 4680 batteries to power other vehicles, most
notably the $25,000 small car the company is scrambling to launch by the
mid-2020s.
Tesla has some limited production capacity for 4680 cells in Fremont,
California but its plant there is mainly for pilot production.
Panasonic, one of Tesla's long-standing battery suppliers, is planning
to build at least two plants in the United States but has only just
broken ground on the first.
Two of the nine people familiar with the matter believe Tesla's progress
with scaling up 4680 production will likely gain steam, especially once
it achieves stability with the production know-how on one production
line.
[to top of second column] |
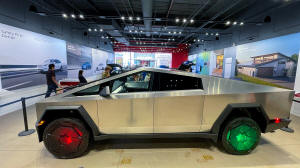
Tesla's new Cybertruck is shown on display at a Tesla store in San
Diego, California, U.S., December 9, 2023. REUTERS/Mike Blake
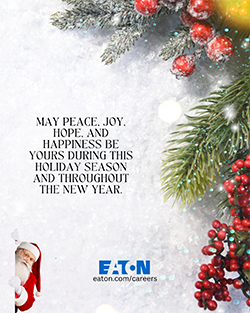
They said Tesla had been focusing on establishing robust know-how to
produce batteries without flaws first time round. It's a
time-consuming process but, "once you crack the code and establish
stability, it is like exponential", one of them said.
"Speed would pick up. There is already a lot of traction in dry
coating," the person said.
Tesla's battery tsar Drew Baglino said in October that the company
was now producing 4680 cells on two production lines in Austin and
plans to install a total of eight lines there in two phases, with
the last four due to be running in late 2024.
Still, one of the two people said replicating established know-how
from one production line to the next is no cakewalk.
The source said only about 5% of cells made on profitable production
lines are ditched but scrap rates could shoot up to 30%-50% and
hover there for several months as each new line gets going.
One of the sources said Tesla's dry-coating method for cathodes was
not proving to be any faster than the old wet process, though scrap
rates had dropped to as low as 10% to 20%.
Baglino did not respond to requests for comment for this story.
'GOOEY MESS'
The sources said Tesla was struggling to mix the cathode materials,
which include lithium, manganese and nickel, with a binder and stick
them to a metallic foil to produce a cathode - without using
moisture.
Two of the people said the process worked for small amounts but when
Tesla tried to scale it up, a lot of heat was generated and this
melted the binder, which one of the sources believed was
polytetrafluoroethylene, more commonly known as Teflon.
"If you melt the glue, pretty soon everything will become one big
chunk of gooey mess," another of the sources said.
Equally problematic for Tesla are the machines used to coat the
metallic foil to produce battery electrodes - equipment which is
akin to huge magazine and newspaper printing machines with large
rollers, the sources said.
To accelerate cell production, Tesla is trying to coat multiple
strips of magnetic foil with active battery materials at the same
time, and at high speeds.
That calls for large, wide rollers, as well as applying tremendous
force to press the materials onto the foil. But because the rollers
are large and wide, applying pressure evenly is proving to be a
challenge, the sources said.
And when pressure is not applied evenly, Tesla gets electrodes with
uneven surfaces and thickness, which are no use for its battery
cells and need to be scrapped, the sources said.
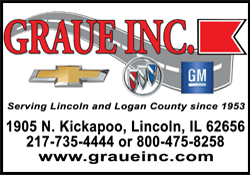
Perhaps more problematic, Tesla's Baglino told a fireside chat at a
battery conference in March that Tesla was still building a
completely new quality verification system so they could weed out
cells with flaws in coating.
One of the sources with knowledge of the matter, said specifically
it was about building data infrastructure around Tesla's battery
development, manufacturing and in-field use because in some cases
the flaws were hidden in the coating and did not show up for a few
months down the road.
In other words, Tesla doesn't quite know yet which dry cells are
good, and which ones need to be junked, the source said.
(Reporting by Norihiko Shirouzu in Austin and Paul Lienert in
Detroit; Editing by David Clarke)
[© 2023 Thomson Reuters. All rights
reserved.]
This material may not be published,
broadcast, rewritten or redistributed.
Thompson Reuters is solely responsible for this content. |