Accelerated manufacturer skills training
program launches
Five credentials offered to advance
qualifications
Send a link to a friend
[September 24, 2014]
LINCOLN - On the 19th, a group of eight
individuals were given a tour of the Eaton facility as part of a new
accelerated training program. Accompanying the individuals were the
instructors that will be working with the trainees over the next
eight weeks.
|
The program is being overseen by a collaborative effort between
Eaton, Heartland Community College, and the Land of Lincoln
Workforce Alliance. This project has been made available by a grant
from the United States Department of Labor. The goal of the program
is to provide qualifications and skills for those wanting to join
the manufacturing industries and fill a growing demand for laborers
in the job market.
Larry Peterson, project manager for the Central Illinois Advanced
Manufacturing Partnership, said that the eight week program will
“equip trainees to enter the workforce with five industry recognized
credentials from the Manufacturing Skill Standards Council.”
According to Anne Schneider, the Executive Director of Workforce
Alliance, recruitment for the program started in July. The five
credentials are Safety Practices, Quality Improvement, Manufacturing
Processes, Maintenance Awareness and the Certified Production
Technician credential (or CPT credential).
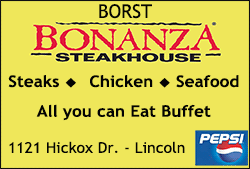
“Earning the CPT credential is the first step in filling the skills
gap many manufacturers are experiencing,” according to Peterson.
The tour was led by Patti Becker, the hiring manager at Eaton. “This
is a great opportunity for those in the program,” said Becker.
Becker said that the training program was put in place partially
because there have been so many applicants coming to Eaton recently.
Becker said that a lot of the applicants found out about the
training program through the Land of Lincoln Workforce Alliance.
The tour began with a showing of what is produced at Eaton and some
information as to what kind of careers the trainees can expect to
see. “Ninety nine percent of our applicants start in assembly,” said
Becker. Becker said there are about 85 employees on the first shift,
60 on the second, and 40 to 50 on the third shift. “The third shift
has been increasing lately,” said Becker.
Becker also explained the number of other opportunities for training
after the trainees begin, such as apprenticeships or the five-year
programs led by Heartland Community College.
[to top of second column] |
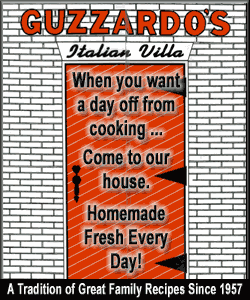
Trainees were then led through the assembly areas of the
factory. They were shown that assembly areas include monitors
with assembly diagrams and images with safety requirements as
shown.
Becker also showed the trainees the automated assembly area. “We
don’t have a second shift in automated yet,” said Becker.
Austin Grammar, Heartland’s Training Coordinator, said that the
eight week program will include the equivalent of what is
normally taken in one or two semesters of normally scheduled
classes. The classes that make up the program will take place
daily beginning at 5 p.m. in the evening and last four hours.
The instructors are provided by Heartland. Each class will
involve lectures and hands-on learning.
According to Bill Thomas, the interim director for the Lincoln
and Logan County Development Partnership, "Helping ensure our
area manufacturers have a pool of qualified workers is one of
the more important things we need to focus on when working to
improve Logan County's economy.”
[By DEREK HURLEY]
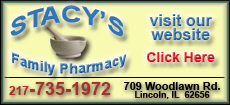
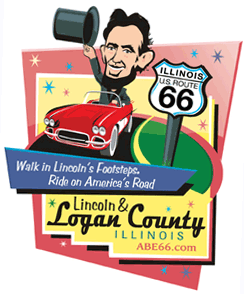 |