"The biofilter process is fairly well established and has
been used for years," said Ted Funk, University of Illinois
agricultural engineer. With the right combination of organic
material, odors can be reduced by as much as 80 percent, he said.
Funk and his colleagues are also working on an automated system that
will maintain moisture content in the filter. A biofilter is a bed
of wood chips or other organic material connected to a livestock
building ventilation system or manure storage with air ducts.
Exhaust fans push the air coming from the building or storage up
through the organic material, and bacteria and fungi that grow there
remove the odor-causing components by using them for food.
In their U of I work, Funk and his colleagues used a biofilter to
reduce odors coming from the headspace of an in-ground manure tank
on a hog farm in western Illinois. Two filters using two different
media were placed side by side. One filter used a debarking product
(tree bark and dirt), and the other used wood chips and hay.
Air samples from each biofilter were collected and sent to an
olfactory group at Iowa State University. This panel of eight human
"sniffers," trained to judge the presence of odor, rated the overall
odor strength of each sample.

"The debarking product worked better than the wood chips and hay
to reduce ammonia," said Funk. "However, both media were pretty
effective in odor reduction on the average."
For a biofilter to work properly, Funk said the organic material
must remain moist, or the organisms will die off and the air remains
untreated.
"The established method to monitor moisture content in the filter
is to reach your hand in, grab a sample and see if it feels all
right," he said. "It's kind of hard to get farmers excited about
doing that."
So Funk and his colleagues went back to the lab to develop an
automatic system that would control moisture content.
[to top of second
column in this article]
 |
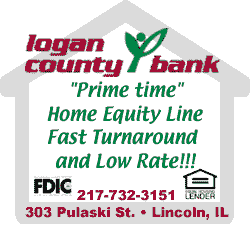
"We wanted to produce a moisture-sensing technique that would
give a readout of the moisture percentage in the filter and also
trigger an electronic control to turn water on and re-wet the filter
when it needs it," Funk said.
After testing a variety of moisture meters, they found that a
relative humidity meter worked best at detecting a drop in moisture
content. However, a relative humidity meter is essentially connected
to a little tube and can only test one spot at a time. So Funk and
his crew are building a much larger sensor -- about 30 by 36 inches
-- out of a hog panel grid.
"We stack three grids together to form a capacitor," Funk said.
"The top and the bottom grid are grounded, and the one in the middle
is energized at a high frequency. We bury it in our biofilter medium
and determine the moisture content. When the moisture reading goes
down below a certain level, the control circuit triggers a switch to
turn the water on.
"Then the reading goes back up and the process repeats itself,
irrigating the biofilter as needed. The farmer doesn't have to worry
about sticking his hand down in a dozen places to see if it's wet
enough.
"The bottom line is, if we can get this to work at a relatively
low cost, there will be a lot more use of biofilters on hog farms.
And that will greatly reduce the amount of odor emitted, which will
make everyone happy."
For more information on biofilters, read the "Livestock Waste
Facilities Handbook," published by MidWest Plan Service. Section 3,
"Outdoor Air Quality, Manure Management Systems," offers good
general information on how biofilters are made and work to reduce
odor. The book is available from MidWest Plan Service at
www.mwpshq.org or by calling 1
(800) 562-3618.
[News release from the
University of Illinois College
of Agricultural, Consumer and Environmental Sciences]

|